Opening any modern electronic equipment reveals a huge number of tiny components placed on a board. When closely examined, several tracks on the board lead to and from the components. The most common example of this is a computer motherboard—several hundred components crammed onto a board measuring roughly 23 x 23 cm. The board holds the tiny components together, some of them little larger than a grain of sand. PCB Trace Technologies Inc. manufactures such boards, popular as printed circuit boards, and the components are either surface mount components (SMC) or through-hole components (THC).
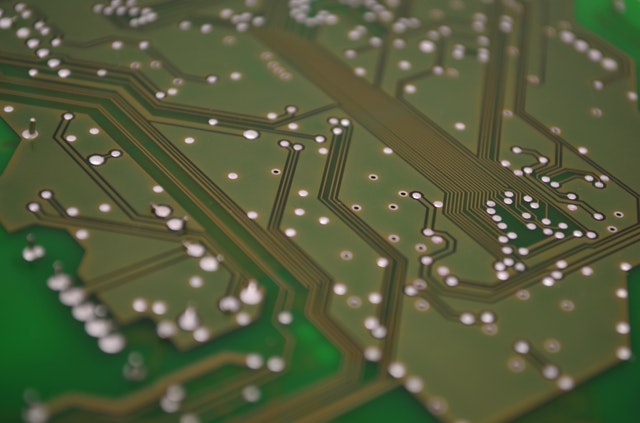
Why Printed Circuit Board is Necessary
Most equipment with complex functionality use a multi-layered printed circuit board. The need for such a board is obvious—placement of all the components and interconnecting them so that the equipment can function as intended. This would very well be impossible if not for the presence of the printed circuit board. Therefore, summarizing the necessity for a printed circuit board, it provides:
- Suitable mechanical support for most of the components
- A means of electrically interconnecting the components
- Necessary shielding and isolation for sensitive circuits
- A means of properly distributing voltage and power to different sections of the circuitry
In specific cases, an electronic circuit board may have additional functionality like aiding heat removal, acting as a waveguide for high-speed signals, and acting as a replacement for wire harnesses.
Depending on the application and its complexity, PCB suppliers provide a variety of board types:
- Single-Layer Boards
- Double-Layer Boards
- Multi-Layered Boards
Again, various applications may require specific makes of boards such as including:
- Rigid Boards
- Flexible Boards
- High Definition Interconnect Boards
- Metal Clad Boards
- High-Speed Boards
- High-Frequency Boards
However, before PCB manufacturing and assembly, it is necessary to design a PCB.
PCB Circuit Design
PCB Trace Technologies Inc. recommends before starting on a PCB circuit design, a designer must gather some important and necessary equipment and information. These include:
- A Computer-Aided Design (CAD) Software Package for PCB design
- A Schematic
- A Bill of Materials
- An Outline or Layout
- A Component Library or Component Dimensions
- Design Rules
PCB CAD Software Package
It is perfectly possible to design printed circuit boards without using computers, but the use of computers makes the process significantly simpler, and error-free. Moreover, changes in design are easier to implement on a digital medium rather than if the design is on paper. Multiple CAD software packages are available in the market, some free to use and others require a purchase. They are also known as EDA or Electronic Design Automation tools.
Few examples of free PCB CAD software packages are:
- Eagle
- KiCAD
- Pad2Pad
- EasyEDA
Some examples of non-free PCB CAD software packages are:
- Proteus Design Suite
- Altium Designer
- Cadence OrCAD
- PADS PCB
Most of the above PCB CAD software packages provide three basic functionalities:
- Schematic Entry
- Component Layout
- Track Routing
In addition, it is possible to interface them to a mechanical CAD system like AutoCAD for the mechanical layout part. Some of the packages come with a built-in component library, but others may require it to be a separate purchase.
Schematic Entry
As the name suggests, a printed circuit board is the printed version of an electronic circuit on which the assembler will mount components. Therefore, the initial requirement for a PCB circuit design is an electronic circuit or a schematic. Manual drawing may work for simpler circuits, but drawing a schematic with the help of a PCB CAD software package makes the process more effective for the designer. The steps for a schematic entry are:
- Symbol Placement
- Interconnections
- Component Specification
Symbol Placement
The CAD provides a library of line drawings or symbols representing various electronic components. The designer can download symbols for specific components and place them in the workspace. The package provides each symbol with an individual reference designator.
Interconnections
The CAD package provides a means for interconnecting components according to the actual electrical interconnections. A line will appear when interconnecting the pins of two components. Usually, a dot where two lines cross represents an electrical connection. The software package records each interconnection and can furnish a net-list—a text-based list of the interconnections for future reference and cross-verification.
Component Specifications
The designer must specify further details about each component they have used in the schematic. This includes the manufacturer’s part number and the package specification.
Bill of Materials (BOM)
Most CAD software packages have the capability to provide a printable list of all components the designer is using in the schematic. This usually contains the reference designator, the component type, its package information, and the manufacturer’s part number at the minimum. A BOM is useful for further processing such as purchasing components and for assembly.
Outline or Layout
A printed circuit board typically fits inside a mechanical enclosure, and therefore a defined outline or layout of the board is necessary. The designer must make sure all components remain within the boundary of this layout so that after assembly the board and components fit the enclosure.
Component Library
The designer now transfers the schematic into the layout. For this, designers make use of the component library. The component library is a database of various footprints of components linked to their manufacturer reference and package type. This is necessary because manufacturers offer the same component in different packages. The footprint is a two-dimensional mechanical drawing of the component package.
After downloading the footprints within the layout boundary, the software package can arrange them in the best possible manner. The designer can manually alter the component layout to suit required electrical signal flow, power flow, and other constraints.
Design Rules
The final step in printed circuit board design is routing. Most CAD packages offer auto-routing as a feature, but also allow manual override. Routing requires transforming all the nets into physical connections that will finally become copper traces. Defining design rules at this stage is important. It allows the computer to flag a warning if there is a violation such as two traces coming closer than the design rules specify, a trace passing next to a pad without adequate clearance in between, or a net inadvertently connecting to another net it should not connect.
While routing, the designer can change the number of layers they need to fully route all the nets while meeting the design rules. At this stage, the designer must also define the necessary isolation and shielding for sensitive circuits. They do this by assigning specific layers as power or ground shields. They also must provide proper tracks for power delivery to different parts of their circuit. To interconnect different layers as necessary, designers use special features known as vias. The CAD package shows tracks on various layers in different colors to make it easy for the designer to differentiate between them.
Once the designer has finished routing the board, they must use an industry-standard output software known as Gerber to translate the design files into proper manufacturing files. Circuit board fabrication services use these Gerber files to fabricate the printed circuit board.
Conclusion
PCB circuit design is at the heart of all PCB manufacturing and assembly. PCB Trace Technologies Inc. advises designers to be very careful during the design phase, as it affects the circuit board price, and ultimately, the overall success or failure of the entire project.