Introduction
Reverse engineering is a common technique in the engineering industry. Its basic purpose is to study a device or a mechanism to enable a deeper understanding of the device’s functioning and design principles. When applied to a PCB, the technique helps in studying the layout in its various layers to recreate its fabrication data. Historically, companies have used reverse engineering to assess their competitor’s products. The most famous case of the earliest reverse engineering was possibly by Galileo who made his own telescope based on the information he gathered about one made by the Dutch eyeglass maker, Hans Lipperhey. As such, PCB reverse engineering is a valuable tool in the modern electronics industry and serves various applications. PCB Trace Technologies Inc. brings you a comprehensive guide to PCB reverse engineering.
Definition of PCB Reverse Engineering
Reverse engineering of a printed circuit board is the process of generating its fabrication and design data as accurately as possible.
Legal Framework and Ethical Considerations
The first question that may arise regarding PCB reverse engineering is, whether the process is legal and ethical. Due to the typical negative nature of the term “copy” people wonder about its legal status. However, the reality is that PCB reverse engineering is a widely accepted technique as it offers ample opportunities for learning and at the same time, speeds up the product development time.
To avoid legal risks, one must understand that PCB designs are governed by intellectual property laws such as the Copyright Directive and DMCA or Digital Millennium Copyright Act. Any type of analysis and research on a PCB should have its basis in legally obtained information and not through disclosures or misappropriation of the trade secrets of others.
That said, several legitimate applications allow fair use and legitimate purposes for PCB reverse engineering.
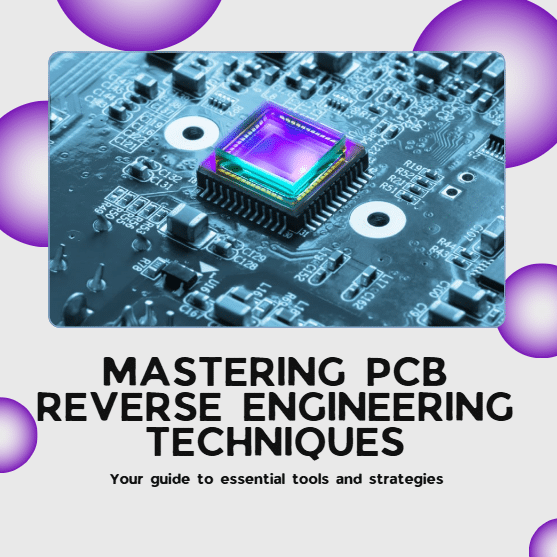
Legitimate Applications for PCB Reverse Engineering
End-of-Life Component Replacement
At times, it may be necessary to replace an end-of-life component in an important PCB that is performing a necessary function. If an exact replacement is not readily available, it may be necessary to use the closest component in functionality. In most cases, there will not be a pin-to-pin matching, requiring a redesign of the PCB layout to accommodate the new component.
Unless the fabrication and design data of the PCB is readily available, engineers may have to rely on reverse engineering to save time.
Legacy System Maintenance
Contemporary PCBs in legacy systems often do not carry documentation regarding their design or fabrication data. Most of the time, systems sourced from other countries arrive with very little or no information at all. Organizations need legacy system reverse engineering to handle unexpected downtime of their expensive systems.
Operators need expert help to solve issues when maintaining legacy systems. Often, there are no professionals readily available with the special expertise to handle the situation. This lack of knowledge about the system can put a company on the bind. With reverse engineering, they can generate crucial information, spotting areas that could result in a problem, and not have to rely on an external professional.
Failure Analysis and Debugging
OEMs often want to find ways to improve their products, making them more effective over their competitors. By reverse engineering their competitor’s PCB, they can debug and analyze weaknesses in it. This information may prove to be invaluable in improving their own PCBs, thereby reducing the time-to-market for a more effective product.
For instance, a competitor’s PCB may be expensive. Through reverse engineering, it is possible to determine whether the high price is because of technical reasons or due to a lack of competition. This knowledge could be helpful in designing a PCB costing much lower, thereby attracting customers.
Security Research and Vulnerability Assessment
Businesses need to understand both the accessibility of competitor PCB reverse engineering and the safety degree of their own PCBs against hacking attempts. For this, they may conduct competitions inviting people to reverse engineer or hack their PCBs to learn about the weaknesses in their products. Manufacturers can leverage this data to fix weaknesses within their products which makes their products more potent.
Competitive Analysis
OEMs often conduct a market research before deciding on the product they want to market. Once decided on the product, they must assess the present competition. Reverse engineering is one of the tools companies popularly use to analyze the competition. The knowledge helps them to design a product that has an edge over their competition.
Educational Purposes
Companies designing PCB design software often indulge in reverse engineering to understand different methods that industries use for designing their PCBs. This serves as an educational exercise to help them design software that circumvents hurdles their users may be facing.
PCB Reverse Engineering Methods
Primarily, there are two major methods for reverse engineering PCBs—Non-destructive techniques and destructive techniques. Various techniques are useful here, and most require removal of all components from the board before starting. We will discuss them one after the other.
Non-Destructive Techniques
As the name suggests, this method allows the PCB to be reused after the reverse engineering process is over. That means, once the reverse engineering study is concluded, the components can be re-soldered on the board, and the assembly functions as it originally did.
Visual Inspection
This is the most basic technique to study a PCB. The operator often uses a strong diffused light and a high-power magnifying lens to study the PCB. However, as this method uses visible light, the visual inspection method is severely restricted to the outer surfaces of the PCB. That means this method cannot inspect the inner layers of a multi-layer PCB.
X-Ray Imaging
Where visible light cannot reach, X-rays can. X-rays can penetrate the substrate and reach the inner layers. Therefore, X-rays can produce 2-D track images from the inner layers. This is good enough for multilayered PCBs as long as there are only a few layers and the routing density is not very high. For a high number of layers with dense routing, the images of the inner layers may be too complex to decipher.
3D Scanning
For complex high-layer number PCBs, it is customary to use 3D scanning using X-rays. The method is similar to CT scans used by the medical industry. Recording images of thin sections of the PCB cross-section provide detailed information on structure of the inner layers.
Electronic Testing and Signal Analysis
Often, monetary constraints limit the investigation techniques used during the reverse engineering process. Not everyone has access to X-ray imaging systems or afford 3D scanning. The best bet here is to use electronic testing and signature analysis.
For instance, a copper track on the top surface may be connected to several others. However, the interconnections may not be apparent as part of the track is buried in inner layers. Testing for electrical continuity is a simple but sure method of detecting such interconnections.
However, modern PCBs often have passive components embedded in their inner layers. These can often lead to misinterpretation of continuity results. However, using a process like signal analysis it is possible to determine the presence of such embedded components. The testing process involves signal generator waveform input at one track while an oscilloscope tracks output changes at different test points. A modified waveform detected gives a clue to the type of the embedded component within the PCB.
Destructive Techniques
As the name suggests, destructive techniques render the PCB non-usable after the application of reverse engineering techniques. Therefore, if the technician must apply more than one technique, they will need as many quantities of the PCB.
Cross-Sectioning
A microscope provides visibility of the multiple layers within a PCB when observing its cross-section. Identification of the layers is an important step before separating them for further examination. Layers in a PCB typically refer to the physical stack-up of copper tracks, pre-preg, substrates, solder masks, and silkscreen layers. However, for reverse engineering, the most important layers are the copper tracks and substrates. Cross-sectioning effectively reveals details about them. Operators can then apply various methods to separate them for individual study.
Layer Separation
Unlike peeling an onion, it is not possible to peel away the different layers of a PCB entirely. Operators use precision techniques to remove a layer to expose the one beneath it. Once they have finished studying it, they can remove it to expose the next layer. Three popular methods are in use—sanding, chemical deprocessing, and micro-etching.
Precision grinding operations or milling methods remove the top layer of a PCB to expose the lower layer during the sanding process.
Chemical deprocessing achieves the same result, but only by using chemicals to strip the uppermost layer.
Where it is not necessary to remove the entire layer, operators use micro-etching to remove the top layer from a part of the PCB.
Tools and Equipment in PCB Reverse Engineering
Operators use various tools and equipment for reverse engineering PCBs. The implementation utilizes both hardware equipment and software solutions which include:
Hardware Tools
- Desoldering and Rework Stations — Primarily for removing components from the board.
- Signal Analyzers and Oscilloscopes — For non-destructive identification of embedded components within the PCB’s layers.
- Microscopes and Imaging Systems — For detailed examination of layers and to record and document them.
- X-ray Machines — For examining the inner layers and documenting them.
Software Tools
- Image Processing Tools — For converting the images captured to the proper format for further processing by PCB layout software.
- PCB Layout Reconstruction Software — For tracing all visible design elements and recreating the layers digitally.
- Schematic Capture Tools — For generating schematics from the interconnecting diagrams obtained from track layout and component footprints.
- Circuit Simulation Software — These are useful for verification and validation of the schematic and layout generated during reverse engineering.
Step-by-Step Process in PCB Reverse Engineering
Initial Documentation and Photography
PCIB reverse engineering procedures start with capturing either a drawing or scanning or photographing of the assembly. This is an important step if the PCB must be reassembled later, as it records the position and orientation of all components on the PCB. It also helps in component identification and mapping, and in preparation of a BOM or bill of materials of the board.
Using good lighting and a high-quality camera is important as these will help to capture every detail. It may be necessary to perform color switching and or image editing to further enhance the details of the components.
Signal Trace Analysis
This is the second step before stripping away components from the board. The operator injects various signals at board inputs while recording the waveforms at the outputs. The collected print will function as an identification fingerprint that allows board analysis or provides aid after assembly. Needless to say, the more detailed the signal trace analysis is, the more useful it can be at later stages.
Component Removal and Desoldering
Once the initial documentation, photography, and signal tracing is completed, the operator can proceed to remove the components by desoldering them. At this stage, it is important to catalog each component removed, by its designation as marked by the silkscreen on the board. This will aid in the BOM preparation, as it may be necessary to remove the silk screen and solder mask for further processing.
Layer Stack-Up Analysis
After removing the components and desoldering the board, it may be necessary to strip the silkscreen and the green solder mask from the topmost surface of the board. This will expose the top and bottom copper layers, which the operator can subsequently photograph for documentation and recreation.
If the board has multiple layers, it may be necessary to expose and image inner layers by using X-rays. For complex PCBs, the operator may have to resort to destructive techniques for exposing and imaging the inner layers. The objective is to gather as much detail as possible about each layer to help in the reconstruction.
Reconstruction
There are primarily two objectives in the reconstruction process. One of them is the schematic reconstruction, while the other is the layout reconstruction.
Schematic Reconstruction
The objective is to create a netlist or a diagram of interconnections between each pin of all the components. This can serve as an input to the schematic capture tool along with the footprint of the components to serve in the effective reconstruction of the schematic.
Layout Reconstruction
This may serve as an important step if the objective is to make a close reproduction of the board. A suitable PCB layout software is necessary here, to convert the images of different layers into the layout diagram. The PCB layout software can add the necessary vias and copper planes to complete the layout.
Finally, generating a netlist can assist in cross-verification with the netlist generated by the schematic reconstruction step to correct any mistakes.
Design Verification
This is the final step in verifying the reconstruction process. A circuit simulation software program is very useful here. It helps to cross-check if the reconstructed circuit has the proper interconnections necessary for it to function as intended.
Challenges and Considerations in PCB Reverse Engineering
Multi-layer Board Complexity
This is the first major challenge to consider during PCB reverse engineering. Without studying a cross-section of the PCB under a microscope, it may be impossible to know the number of layers it has.
The second major challenge may be to reconstruct individual internal layers. X-ray imaging helps but only to a certain extent. The more densely crowded the layers are, more is the difficulty for the X-rays to differentiate between tracks of one layer from the others.
The presence of solid ground or power layers compounds the problem further, as they do not allow X-rays to pass through. Consequently, layers adjacent to the solid ground or power layers are difficult to image properly.
Component Identification
OEMs are always keen to protect their intellectual properties, and for this they try various methods to prevent their know-how from being discovered by their competitors. For instance, they may replace a part of the circuit with an ASIC, not available in the general market.
Encapsulation
Other methods to safeguard intellectual properties may involve encapsulating part of or all of the circuit with hard epoxy. Typically, this epoxy may be impossible to remove without damaging the board or its components, thereby severely denting the reverse engineering process.
Hidden or Embedded Components
Using hidden or embedded components serves a dual purpose. First, they help to increase the real estate available on the board for routing. Second, they help in preserving intellectual property by making reverse engineering that much more difficult.
While it may be possible to gauge the presence and estimate the value of an embedded passive component by signal trace analysis, the presence of a second component in series or parallel can complicate the measurement significantly.
Signal Integrity Analysis
Reverse engineering PCBs is not complicated as long as the board is a single- or a two-layer type and working with low frequencies. Multi-layered boards that function at high frequencies represent a substantial challenge for such testing methods.
Special geometric requirements must be implemented to meet signal integrity targets within a pair of traces. The spacing between the two, and their distance from a power land or ground layer may be defined to generate a specific impedance. Again, the length of one of the traces may have been trimmed to adjust its impedance. These factors may not be initially apparent to the person reverse engineering the board, and consequently, the derived board may not function as intended.
Modern Board Technologies
The production of versatile PCBs relies on modern technologies which include HDI or High-Density Interconnect along with Flex or flexible circuits. PCB manufacturers achieve functional and operational goals by using multiple materials. These factors may not be immediately apparent when reverse engineering the board and may lead to complications.
Best Practices for PCB Reverse Engineering
Data Organization and Storage
It is highly recommended to have some form of QMS or Quality Management System established in the organization. This allows for standardized documentation and storage methods according to the established quality control procedures. This is important as all employees can then follow the reverse engineering process and avoid ambiguity.
Safety Considerations
Safety requirements should always supersede the acquisition of results through reverse engineering procedures. The organization must allow proper safety margins for all engineers to follow, for instance, track and component spacing according to operational voltage difference. This practice will help to avoid unnecessary mishaps on the production floor.
Project Planning and Management
This is a very important step for organizing the PCB reverse engineering process, bringing it to a logical conclusion, and reaching the market on time.
Future Trends
Advanced Imaging Technologies
3D scanning technology is one most significant advancements for reverse engineering PCBs. Structured light and laser beams enable the technology to retrieve board geometry for digital modeling. The technological system enables users to obtain exceptionally precise details and measurements.
AI and Machine Learning Applications
A paradigm shift is happening in the field of reverse engineering with the integration of AI and machine learning. AI algorithms can analyze data at tremendous speeds, At the same time, feedback through machine learning helps improve the accuracy of these analyses.
For instance, an AI system operating on a 3D PCB scan detects the included materials to improve reverse engineering operations with enhanced precision and efficiency.
Automated Reverse Engineering Tools
The new technology of Automated reverse engineering tools with VR or Virtual Reality stands as a leading emerging innovation today. The virtual reality technology produces a 3D PCB representation that enables engineers to access the board during virtual interactions. Engineers use tests to duplicate various conditions to observe how designs perform during simulations.
Another advantage of VR is it allows testing the reverse-engineered PCB. While testing, engineers can simulate different conditions to observe the performance of the design. They can then make necessary changes to the layout before producing a prototype. Such implementation tools decrease both design duration and test and prototype expenses.
Emerging Board Technologies
Manufacturers are now tying PCB reverse engineering with 3D printing or additive manufacturing. As these technologies advance, the integration between PCB reverse engineering and the additive processes for manufacturing PCBs is going to increase further. This allows engineers to make prototypes more quickly based on reverse-engineered PCB designs.
Conclusion
Many organizations use reverse engineering to gain clarity about highly complex PCB design processes and fabrication methods. Although there is a scope to misuse the process for illegally usurping intellectual property, PCB reverse engineering can enhance technical knowledge and reduce design time significantly. Our team at PCB Trace Technologies Inc. has compiled an extensive overview of PCB reverse engineering technologies along with their methods and tools and assessed their prospective development. Used legitimately, PCB reverse engineering can be a powerful tool for engineers to reduce their time and effort during design, thereby cutting short their time-to-market.