Recent component supply-chain disruptions all over the world have placed OEMs in a tough position for predicting the demand and supply of electronic products and systems. Despite possessing historical sales data and the latest market information, OEMs are struggling to decide how much of a product variant to stock. They are trying to predict the order from customers over the next 12-month period, as they do not want to stock too many of the wrong variant.
From consumer products to complex industrial electronic products, customers are increasingly expecting better service. OEMs are responding to this requirement by becoming agile, as they stand a better chance of survival when they can respond rapidly to customer demands. Although one of the methods OEMs are adopting for increasing their agility is outsourcing to a contract manufacturer, they are also resorting to postponement manufacturing. As an eminent contract manufacturer, PCB Trace Technologies Inc. also offers postponement manufacturing services to our OEM customers.
Postponement Manufacturing
Under postponement manufacturing, we build generic versions of the product for our customers and stock them as embryo units. As and when we receive a firm order from the customer, we take out the embryo units from the stock, configure and test them, and package and ship them to the customer.
For instance, we build PCBs for an OEM customer who sells various types of robots. The PCBs for the robots have about 95% component commonality. We assemble and stock these PCBs with all the common components mounted. Depending on the order from the customer, we mount the balance components, configure the PCBs, test them, and deliver.
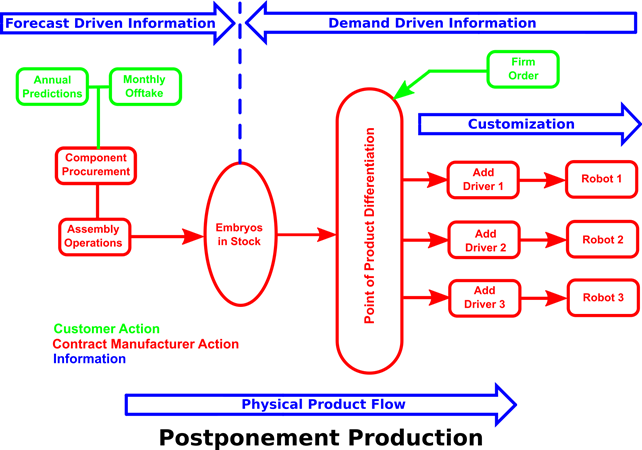
In fact, this is not a recent idea. In the 1990s, Dell Inc. started this method of manufacturing for improving their supply chain efficiency and shifted the manufacturing industry norm from make-to-stock to make-to-order. Dell was able to reduce cycle times significantly, allowing the company to reduce their inventory of three to four weeks to just a few days.
Preparing for Postponement Manufacturing
Although, in theory, postponement manufacturing looks relatively simple, practice of this technique requires a very close collaboration between the OEM and the contract manufacturer. The CM must keep ready enough embryo units to meet the demand from the OEM, and for this the CM requires an indication of the entire quantity of finished products the OEM requires per annum, along with a typical monthly offtake. The OEM must also have a robust supporting supply chain.
As a contract manufacturer, PCB Trace Technologies Inc. offers our customers full turnkey assembly services. We take care of the entire process of PCB fabrication, component sourcing, component assembly, testing, packaging, and shipment to the customer. As we also have a strong supply chain setup, we are in the best possible position to help our customers prepare for postponement manufacturing.
Typically, we execute a service level agreement with our customers to capture the requirements in clear terms of stock liabilities and delivery expectations. Although it is not possible for our customers to predict the exact variations they require at the beginning of the year, they provide an estimation of the total number of units they plan to sell during the year. This allows us to make an estimate of the stock levels we need to keep ready in our stocks to meet their potential demands.
For postponement manufacturing to work successfully, we arrange regular business meetings with our customers to discuss the stock liabilities and finished goods levels. The meetings are also an opportunity for the customer to update us with any changes they may have with their forecasting.
The business meetings are also a forum for discussing dropping of old products and additions for new ones. Both scenarios require making significant changes to the existing supply chain, to ensure that neither the customer nor PCB Trace Technologies Inc. has any excess raw materials.
Benefits of Postponement Manufacturing
Postponement manufacturing can be substantially beneficial to our OEM customers, especially if they have elected to engage our full turnkey assembly services. Major advantages they can expect are in the areas of:
Inventory: The major benefit that our OEM customers can expect from postponement manufacturing is a substantial reduction in finished goods stock. As we hold the semi-finished goods for them, we can finish, configure, test, pack, and ship them finished goods as and when we receive a firm order. Our OEM customers do not need to build their stock waiting for their customers to order.
Time-to-Market: Depending on the complexity of the product, typically, this could take from a few weeks to several months to fabricate, assemble, test, package, and ship, beginning from scratch. By adopting a postponement manufacturing strategy, we help the customer split their manufacturing into two stages, with much of the work done in advance. As the customer places the firm order, the only lead-time necessary is for making the final configuration, testing, packaging, and shipment—a minor fraction of the earlier schedule. This drastically improves the time-to-market for our OEM customer.
Agility: As the time-to-market drops significantly, our OEM customers can respond quickly to the demands of their customers and fulfil their requirements before the competition can.
Customization: With the age of mass customization shaping the manufacturing industry, our OEM customers can plan for the requirements of their customers in terms of hardware, firmware, software, packaging, and accessories, thereby personalizing their products the way their customers demand.
Conclusion
Although our full turnkey assembly services are for the benefit of all our customers, our postponement manufacturing services benefit most of our OEM customers presently involved in the design and sales of highly configurable and personalized products. While most of these products have a fluctuating demand because of their variant or optional levels, the postponement manufacturing strategy from PCB Trace Technologies Inc. is the answer to allow our OEM customers become agile enough to handle the fluctuating demands.