Regular printed circuit boards have a limited capacity for dissipating the heat that a hot component is generating when in operation. This is because the board typically has only thin and narrow copper tracks. Even when there are regions with large copper lands on the top surface, the mass of copper is not adequate to effectively dissipate heat. It is possible to improve the situation by increasing the copper weight, but that makes the board more expensive compared to a regular PCB. Users typically use external heat sinks to remove heat from hot components. According to PCB Trace Technologies Inc, however, there is yet another option, one using heat sink PCBs.
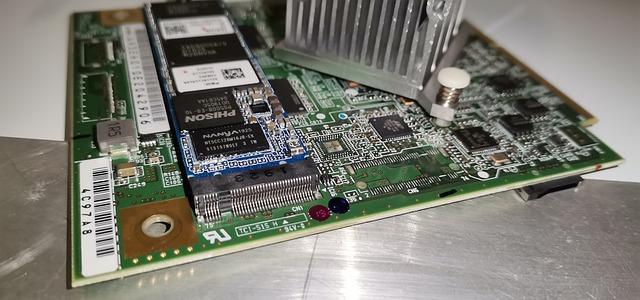
What is a Heat Sink PCB?
Heat sink PCBs are boards with a built-in metal heat sink. The industry calls it metal clad boards. These boards have a thick metal plate acting as a heat sink on one side. The most common and cost-effective heat sink boards are typically singe-sided, although there are double- and multi-layered metal clad PCBs also available.
Single-Sided Heat Sink PCBs
The single-sided heat sink PCB has a thin electrically insulating layer separating the metal plate from the copper traces. The insulating layer has high thermal conductivity to allow heat to pass on to the metal plate. The metal plate is typically aluminum, but some users prefer copper.
Manufacturing a single-sided heat sink PCB is similar to the process necessary for making single-sided boards.
Double-Sided Heat Sink PCBs
Heat sink PCBs in two layers feature PTH or plated through holes in traditional FR4 material or teflon. A separating layer with good electrical insulation properties and high thermal conductivity separates the dual layer board from the metal plate that acts as a heat sink.
Multi-Layered Heat Sink PCBs
Manufacturers use a lamination press for laminating dielectric layers to a metal core. The inner layers may require circuits before laminating them. The outer layers may require further processing, Aerospace and defense applications may require bards with high technology, requiring many lamination cycles for managing buried and blind vias.
Why use Heat Sink PCBs
Although manufacturing heat sink PCBs requires facing considerable challenges, there are several benefits from using metal clad boards.
Passive Heat Exchange
With a large surface area available to dissipate the heat, heat sink PCBs act as passive heat sinks. Components on the PCB that cannot control their temperature can make use of the metal surface on the heat sink PCB to dissipate their heat. This prevents thermal runaway and improves the reliability of electronic boards.
High Thermal Conductivity
Modern applications often require using high-speed PCBs. Although several PCB materials are available that feature excellent low-loss properties including those with low Dk, they lack proper thermal properties for making them function at their optimum. Traditionally, PCB manufacturers have tried to solve this problem by adding copper weight to PCB layers, but this adds significant cost to the manufacturing process of the board. Moreover, this solution also requires adding multiple mechanical interconnects between various layers of the board, making it susceptible to failure.
A metal core on the other hand, helps to minimize the interconnects while providing multiple PTH for connecting with the internal metal core, thereby effectively distributing the heat for dissipation.
Better Thermal Stability
Designing multi-layered boards often requires the designer to handle multiple types of material with various thermal characteristics. The most important characteristic is the CTE or coefficient of thermal expansion for each material. For thermal stability, the designer needs to use material with properly matched CTE along the Z-axis. A CTE mismatch can result in unequal expansion during operation, resulting in hole-wall separation or de-lamination in the PCB. With the metal core removing a major part of the heat, there is less stress on the PCB layers, resulting in better thermal stability.
Better PCB Rigidity
Often, PCBs require withstanding severe shock and vibration for long-term reliability. Metal-cladding allow boards to be naturally more rigid, making them two to four times stiffer than regular rigid or flexible ones.
Heat Sink PCB Manufacturing Challenges
Fabricators typically face critical challenges when fabricating heat sink PCBs. Those with several years of experience have documented these issues and found suitable solutions for effectively and efficiently overcoming these hurdles.
PTH or Plated Through Holes
Generating continuous and uniform hole walls is one of the biggest challenges PCB manufacturers face. This challenge persists for heat sink PCBs as well. One of the basic requirements is removing all debris after drilling the PCB. This ensures depositing a reliable hole wall.
For instance, debris can be Teflon if the manufacturer is using Rogers material, or resin if they are using FR4, and copper fragments from the copper layer. All these materials may stick to the hole wall after drilling. Although most manufacturers use traditional de-smear techniques, it is not an effective process.
It is more effective to use the Plasma Desmear process for cleaning drilled holes in heat sink PCBs. The only metal deposition technique that effectively makes uniform hole walls is depositing electroless copper.
Using Similar Metals
As explained earlier, it is critical to use similar metals with matched CTE or coefficient of thermal expansion for reliable heat sink PCBs. Matched CTE is necessary not only during PCB operations, but also during the manufacturing process, as there are several lamination cycles using application of heat and pressure. In fact, manufacturers may have to add thieving into their production panels to effectively draw away heat.
Tight Tolerances
Although traditional PCBs work with typical tolerances of 5 mil and ±10% for most of their mechanical and electrical features, heat sink or metal clad PCBs require much tighter tolerances. For instance, high speed metal core PCBs may need very tight electrical tolerances close to 1 mil. That means, most mechanical dimensions in heat sink PCBs require CNC machining when routing through metal cores.
Heat Conducting Layer
Traditional methods of removing heat from a PCB required the use of external heat sinks. The popular method used a separately fabricated metal heat sink, attaching to the finished PCB using a traditional pre-preg or liquid adhesive in a lamination press along with pressure and heat.
For a heat sink PCB, the process is somewhat similar, and a lamination press attaches the metal plate to the board with a heat conducting adhesive. These adhesives are available in the form of sheets, requiring a lamination press to attach them using heat and pressure.
Conclusion
Electronic components typically operate within specified temperature ranges. When the temperatures around these components rises beyond the upper limit, they can suffer damage. With excessive heat, the performance of a component may suffer significantly.
According to PCB Trace Technologies Inc, using heat sink PCBs helps in controlling the temperature of hot components by spreading the heat uniformly through a metal plate, ultimately dissipating it to the ambient. The result is a light-weight arrangement, as the use of a metal plate precludes using a heavy external metal heat sink.