PCB Trace Technologies Inc. uses several types of base laminates for constructing printed circuit boards, and these can range from the ordinary paper and resin types to more exotic hybrid materials, with their prices too varying from being inexpensive to prohibitive. In practice, the cost varies mainly depending on a supply-demand relationship for the raw materials and the technology requirement for fabricating the board.
The application and functionality of the design essentially defines the type of material that will go into making the PCB. Most cheap and mass-produced consumer electronic devices typically use a material class FR4.
The industry uses FR4 as a generic abbreviation for Fire Retardant type 4, complying to UL94V-0. The term Fire Retardant usually means that even if the PCB catches fire for some reason, the material does not sustain the flames, and extinguishes them after some time. The UL or Underwriter’s Laboratory tests the PCB material by applying a flame to it and noting the time the material takes to extinguish the flames. The UL defines a time limit, and if the flames persist beyond this limit, the material fails the test. The type number 4 means the material is a laminated epoxy composite, which is again a generic term covering a large spectrum of materials.
FR4 Printed Circuit Boards
For printed circuit boards, the FR4 laminate material that manufacturers such as PCB Trace Technologies Inc. use, is woven glass fabric embedded in epoxy resin. However, the classification of the laminate does not at all depend on the copper cladding that it may have either on one or both its sides. Moreover, the term refers equally to both the laminate and pre-preg materials that make up a multi-layer PCB.
The primary ingredient in an FR4 PCB is the woven glass fabric, making up from 25%-60% of the composition. Next in volume is the resin system comprising epoxy-based compound containing UV blockers and flame retarding compounds. Other materials making the remainder are wetting agents, extenders, and fluorescents.
Glass Fabric
E-Glass or Electronic grade glass predominantly makes up the glass fabric giving the laminate the necessary stability and rigidity. Laminate manufacturers use a fusion of silicon dioxide or Silica and various metal oxides to form the filaments. Each filament is about 5-10 microns in diameter, and the manufacturer bundles about 200 to 400 of these filaments to form a yarn. They weave these yarns together to form the fabric.
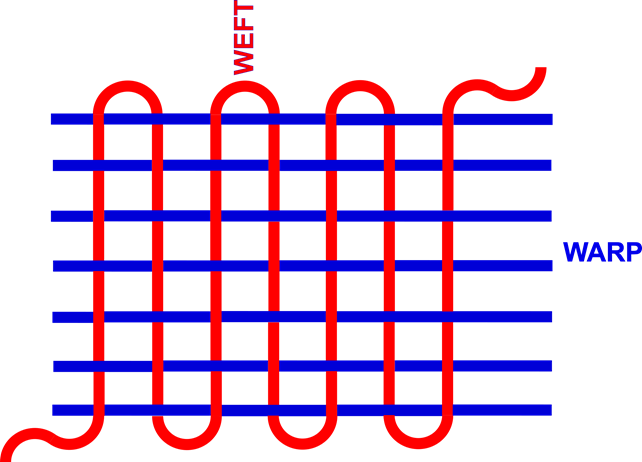
Laminate manufacturers weave the fabric into rolls, with the weave having a warp running the length of the roll, and a waft running across its width. A resin system binds many layers of fabric to make a laminate—a 1.6 mm thick laminate may have up to 8 layers of the fabric.
For pre-pregs, the required thickness defines the number and type of fabric layers after bonding. The resin content may also differ according to the properties necessary.
Resin System
Although the resin system consists of epoxy resin, this is a generic term. Different laminate manufacturers use different formulae to achieve various characteristics. The FR4 technology has been around for long, allowing laminate manufacturers to perfect their processes so they present a marketable product that is consistent and predictable. Variations in the material the laminate manufacturers use offer alternate dielectric properties. Manufacturers also include other additives in the formulations while forming the laminates, and these usually do not affect the finished properties of the material.
Properties of FR4
Properties of the FR4 material selected by PCB Trace Technologies Inc. for fabricating PCBs depends on the application of the PCB in the product and its functionality. Major factors we consider are:
- Dk and Df
- Thermal Stability
The two factors above have a direct bearing on the laminate’s performance regarding:
- The maximum useable signal frequency
- The maximum layer count achievable
- Controlled Impedance parameters
- Presence of Blind and Buried Vias
- Presence of Micro-Vias with Laser Drilling
Dk and Df
Data sheets for different FR4 material available in the market will list these two values. While Dk is the permittivity and Df is the loss tangent of the material, laminate manufacturers state their value for 50% resin content at room temperature. That means the figures will vary with an increase in temperature and increase in resin content.
Dk is the relative Dielectric Constant or Permittivity. This is a property of the material that hinders the transmission of a passing electromagnetic wave. The lower the value of Dk, more is the performance of the material like that of air, as air has a Dk value of 1. Dk of a substrate decreases when its resin content is high, and increases with the rise in temperature.
Df is the loss tangent of the substrate, a property that governs how much energy the material absorbs from a passing electromagnetic wave. A high value of Df implies the substrate will absorb large amounts of energy. This property significantly impacts the attenuation of high-speed signals.
Dk and Df are very important properties of the substrate material, and PCB Trace Technologies Inc. uses them for calculating the controlled impedance at room temperature and with the manufacturers stated values at 50% resin content.
Thermal Stability
Like all materials, laminates also have a Coefficient of Thermal Expansion or CTE that governs the amount of expansion of contraction the material will undergo when the temperature changes. Laminate manufacturers often quote the CTE value up to the Tg temperature—the temperature at which the resin starts to lose its glass like physical state and changes over to an amorphous state.
For FR4, depending on the type of resin and glass content, Tg varies from 130 °C to 190 °C. CTE tends to be loser for laminates with higher Tg.
Read About:
Reducing Automotive PCB Defect Rates
Soft Gold Plating For Gold Ball Wire Bonding
Conclusion
PCB Trace Technologies Inc. uses laminates with predictable and stable values. This gives us a controlled manufacturing process, which we can use safely for repeatable and reliable products.