Soldering is one of the major processes of the printed circuit board assembly. So far, soldering is the only reliable way to attach electronic components to the board without them falling off. In fact, the very existence of printed circuit boards hinges on the process of soldering. Typically, industries use two major types of soldering techniques for assembling components on printed circuit boards—wave soldering and reflow soldering. PCB Trace Technologies Inc recommends knowing the difference between the two, and which type of soldering technique is suitable under what circumstances.
The PCB industry uses the most effective soldering technique for their specific board type. Engineers must make an informed decision on the most effective type of soldering method they will use for their production requirements. This is very important, as their chosen method has a significant impact on the production costs, timelines, and other core elements of the PCB assembly process.
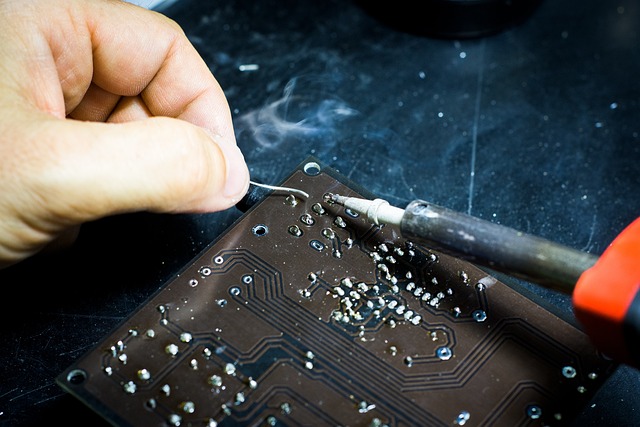
Deciding on the Soldering Technique to use
The PCB industry uses two popular types of components to populate printed circuit boards. These are:
Through Hole Components or THT
These components have characteristically long leads protruding from the body. Mounting these components involves passing the leads through holes in the PCB. This implies the PCB should have pads on the underside of the board for anchoring the leads. Wave soldering is the only way to anchor the leads to the pads.
Surface Mount Components or SMT
The industry developed SMT components to avoid drilling holes in the PCB necessary for mounting THT components. These tiny components have end caps rather than protruding leads. Therefore, PCBs require pads on their top sides for anchoring the end caps of SMT components. Reflow soldering is the only way to anchor SMT components on PCBs.
Wave Soldering Technique
Wave soldering is the bulk soldering process that the industry uses for anchoring leads of THT components under the printed circuit board. A wave soldering machine uses a tub of molten solder over which the board assembly moves on a conveyor. Regulated internal heaters help to keep the solder in the molten condition in the tub. An impeller in the tub pushes the molten solder through a narrow opening so that the solder wells up as a wave. By adjusting the speed of rotation of the impeller, it is possible to adjust the height of the wave so that it just grazes the underside of the board as it passes overhead. The molten solder wets the hanging leads and their pads as the board assemblies pass over the wave. Once the board has passed over, the solder sticking to the leads and pads cools and anchors the component to the board.
There are some prerequisites for good soldering with the wave soldering technique. One of them is preheating, and the other is the application of flux. Preheating is necessary to prevent the board and components from suffering sudden thermal shocks, as the board must reach the soldering temperature of about 260 °C from room temperature.
For preheating, the board assembly moves on a conveyor system through regions of gradually increasing temperature until it reaches the actual wave soldering stage. During the preheating process, a fluxer sprays liquid flux on the underside of the board.
Flux is a liquid chemical compound that, when heated, reacts with the grease and oil on the board surface to remove them. It also helps in reducing the oxides that naturally form on the copper surface. Cleaning the soldering surfaces is important for achieving a high quality of the soldered joint. As the board approaches the soldering zone, most of the flux burns off, leaving the board surface clean.
It is very critical to maintaining proper temperatures in different zones in the wave soldering machine. Failing to control the temperature adequately can mean the board will undergo thermal stresses, leading to cracks and loss of conductivity. Inadequate preheating can lead to the formation of cavities that can compromise not only the board’s strength but also its conductivity. The wrong solder temperature at the soldering zone can lead to dry solder joints and make the board unreliable.
Reflow Soldering Technique
Unlike the wave soldering process that solders components on the underside of the board, the reflow soldering process takes place on the top side of the board. In this process, the preparation of the board assembly is rather different.
The process begins by depositing small amounts of solder paste on the pads of the board. Typically, the operator uses a stencil that has suitable openings for the purpose. Once the paste deposition is complete, a pick-and-place machine places SMT components on the copper pads covered by solder paste. This assembly is now ready to move into the reflow chamber.
Inside the reflow chamber, the board assembly moves over a conveyor system, while infrared heaters raise the temperature of the solder paste until it melts. Molten solder bonds the component’s end caps to the copper pads on the board. As the board assembly moves away from the soldering zone, the solder cools and hardens, anchoring the components on the board.
Similar to the wave soldering activity, good soldered joints in reflow require preheating the board assembly prior to actual soldering. As the board assembly moves through the reflow machine, it passes many preheating zones that gradually increase its temperature to make it suitable for soldering. Unlike the wave soldering process, there is no necessity of spraying the board with flux, as the solder paste already incorporates flux.
Comparing Wave Soldering and Reflow Soldering
Comparing Wave Soldering and Reflow Soldering | |
Wave Soldering | Reflow Soldering |
Requires the use of a wave crest, produced by melting solder in a tub | Requires the use of infrared rays that melt the solder paste |
Complex operation due to internal environment having lower stability | Simplest method of soldering PCBs |
Requires the PCB to have holes for mounting the components | Requires depositing solder paste on the board using a stencil |
Manufacturers can mass produce PCB assemblies, the process being more affordable and time effective | Takes longer time and is more expensive, especially for projects involving large manufacturing |
Producing optimal soldering on PCBs requires manufacturers to consider several factors like pad size, pad shape, board orientation, and many others | More tolerant of pad size, shape, board orientation |
More prevalent for soldering PCB assemblies using through hole components | More prevalent for soldering PCB assemblies using surface mount components |
Why Use Soldering Machines?
While it is perfectly suitable to use manually operated soldering irons to solder components on PCBs, soldering machines automate the soldering process, making it more uniform and less time-consuming. For large-scale production, manual soldering can be impractical from a commercial level.
While the wave soldering technique is most suitable for boards using THT components, and the reflow soldering technique is suitable for boards using SMT components, often there are hybrid boards that require soldering with both techniques.
Hybrid PCBs that use both THT and SMT components require soldering in turn with the wave and reflow process. Typically, wave soldering cannot reach the SMT components on the top side of the board. Similarly, reflow soldering cannot reach the underside of the board for soldering leads of THT components.
Boards that have THT components, may also have SMT components on the underside of the board. Rather than using solder paste, a tiny drop of glue holds the SMT components in place on the underside of the board. It is possible to solder both types of components on the entire board using only wave soldering.
Other boards may have SMT components on the top side along with THT components. Such boards require mounting all the SMT components on the top side first and anchoring with reflow soldering. Once this is done, the board undergoes mounting the THT components and wave soldering to anchor them.
Conclusion
According to PCB Trace Technologies Inc, both options have their individual advantages and disadvantages. Engineers and operators must consider the PCB design and settle for the most optimum method of soldering them.