PCB Trace Technologies Inc makes PCB surface finishes in different types. This is a crucial aspect in PCB manufacturing, as it prevents the exposed copper from becoming oxidized. Surface finish is crucial, as it enables a proper connection between the copper pad and the component over it. Apart from complying with some standard in the PCB industry, the surface finish must also be lead-free.
Exposed copper on a PCB tends to oxidize in air, generating copper oxide that seriously lowers the quality of solder joints. A surface finish stops the copper from oxidizing, thereby guaranteeing excellent solderability along with a corresponding improvement in electrical performance. Increasing market demands on miniaturization, higher reliability and functionability for electronic devices is always pushing PCBs towards making them thinner, light in weight, high density, and higher signal speeds. Therefore, surface finishes must also embrace these upcoming challenges to provide PCBs greater stability and reliability, making them compatible with the above requirements.
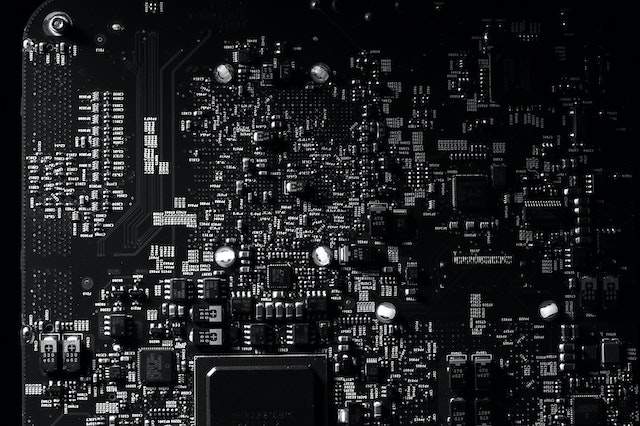
The PCB industry is growing increasingly conscious of environment-friendly sustainable developments. At the same time, issues of environmental pollution related to surface finishes on PCBs are attracting more and more attention around the globe. This has led the EU to implement the legislation of RoHS or Restriction of Hazardous Substances and WEEE or Waste Electrical and Electronic Equipment for eliminating hazardous substances like mercury and lead from electronic products. This calls for green or lead-free PCB manufacturing.
Surface finishes like ENIG or Electroless Nickel Immersion Gold, and ENEPIG or Electroless Nickel Electroless Palladium Immersion Gold not only meet the PCB market’s technological requirements, they also meet the directives of RoHS and WEEE.
While it is difficult for customers to tell the difference between ENIG and ENEPIG, they may also be unaware of which they can depend on. This article about ENIG and ENEPIG discusses their manufacturing processes, and their advantages and disadvantages with an aim to guide users when to use these finishes in specific situations.
Selection Consideration for Surface Finishes
So far, the PCB industry was typically accepting surface finishes like HASL or Hot Air Solder Leveling, OSP or Organic Solderability Preservatives, Immersion Gold, Immersion Tin, ENIG, and ENEPIG. Customers typically base the choice of surface finish for a PCB on considerations for:
- Cost
- Use of fine-pitch components
- Application environment for the end product
- Compliance to RoHS and WEEE
- Probability of high-frequency signals
- Shelf-life of the board
- Thermal resistance
- Shock and drop resistance
- Volume
- Throughput
The above items have their individual significance, and they can never be equally important. Consideration of specific product situation will decide the degree of significance for each item, depending upon specific application.
Why ENIG or ENEPIG?
With PCB development increasingly veering towards finer traces and micro-vias, disadvantages of surface finishes like OSP and HASL became obvious. They had flatness issues and flux elimination issues, for which manufacturers started to use alternatives for PCB surface finishes like ENIG.
However, ENIG had a weakness that results in black nickel boards. Therefore, manufacturers used an upgraded version, ENEPIG. They added a plated palladium layer between the electroless nickel and immersion gold. ENEPIG surface finish is typically a thin layer with a thickness between 0.05 µm to 0.1 µm. Adding the palladium layer stops immersion gold from corroding the nickel layer. This prevents the nickel layer from turning black.
The ENEPIG surface finish also features a highly reliable capability for wire bonding, can withstand multiple reflow soldering processes, and is a switch contact surface. This enables a PCB with ENEPIG surface finish to meet stringent industry requirements, along with the capability of soldering multiple surface mount packages at high density. Because of its advantages, the industry also calls ENEPIG the universal finish. Although more expensive as compared to the ENIG surface finish, ENEPIG offers more opportunities to manufacturers of PCBs with requirements of miniaturization, thinness, and multiple functions.
Advantages and Disadvantages of ENIG and ENEPIG
ADVANTAGES | |
ENIG | ENEPIG |
Easy application process | Excellent for multiple reflow cycles |
Produces a flat surface | Ensures good solderability |
Offers good oxidation resistance | Highly reliable wire bonding capability |
Offers good thermal diffusion | Good as key contact surface |
Long shelf life | Highly compatible with Sn-Ag-Cu solder |
No skin effect | Compatible with multiple package types |
Works on untreated contact surfaces | No black pads |
RoHS / WEEE compliant |
DISADVANTAGES | |
ENIG | ENEPIG |
Affected by plating conditions | |
Affected by process control | |
Affected by thickness of electroless nickel and gold | Thick palladium layer can reduce solderability |
Affected by metal area size in plating bath | Expensive |
Low wettability | Slower wettability |
Easily forms black pads | |
Solder joint reliability low |
Selecting a Cost-Effective Surface Finish
From the advantages and disadvantages listed above, it is typical to select ENEPIG as a better surface finish, with respect to reliability. Although the higher cost of ENEPIG may be a deterrent for some users, its higher quality may offset the cost. Some manufacturers also have solutions for black pad formation while using ENIG surface finish.
ENIG surface finish easily forms black pads. While establishing immersion gold in ENIG, black pads may form due to nickel corrosion. Black pads usually reduce wettability drastically, affecting the solder bonding between copper pad and component. Typically, solder must withstand greater stress when bonding with a corroded nickel surface. Generation of a black nickel surface on the pad will typically break the contact layer between solder and nickel.
With ENIG containing an electroless gold layer, the existence of a black pad is difficult to determine. This is because the gold layer hides the nickel layer, and only a chemical peeling can expose it. Moreover, a phosphorus-rich nickel layer typically forms at the junction of gold and nickel before soldering, and another at the junction of nickel and solder after soldering. However, this does not have any correlation with the black pad formation.
Manufacturers take several measures to avoid black pad formation with ENIG surface finish:
- Electroless nickel solution pH control
- Analyzing stabilizer content of electroless nickel solution
- Stopping nickel surface corrosion during the immersion gold process
New immersion gold technologies help to reduce corrosion of the nickel surface. The pH value of these newer immersion gold solutions is closer to the neutral value of 7. This helps in stopping hydrogen ions from corroding the nickel surface. Moreover, these new technologies use lower quantities of gold, which not only helps to reduce the cost by as much as 50%, but also has a lower influence on the nickel surface.
Applying the present ENIG to flexible PCBs is not acceptable, as the nickel film is not flexible. It will crack when bending the substrate, leading to cracks in the copper layer. However, manufacturers have developed newer techniques of generating nickel films that have a columnar structure. These nickel films have the advantage of generating only micro cracks at their top surface as the substrate bends, and the micro-cracks do not propagate down to the copper layer.
Manufacturers undertake the above measures only to meet customer demands on ENIG surface finish with lower cost but high reliability. ENEPIG surface finish does not need them as it is an upgraded version of ENIG.
Comparing ENIG and ENEPIG Surface Finishes
The distinctive advantages and disadvantages of ENIG and ENEPIG surface finishes lead to different application fields.
COMPARING ENIG AND ENEPIG SURFACE FINISHES | |
ENIG | ENEPIG |
Suitable for lead-free soldering | Suitable for lead-free soldering |
Suitable for Surface Mount Technology | Suitable for THT, SMT |
Suitable for BGA type packages | Suitable for BGA, Press Fit, Wire Bonding |
Suitable for data/telecom applications | Suitable for different PCB packaging technologies |
Suitable for high-end consumer applications | Suitable for aerospace, military |
Suitable for aerospace and military | Suitable for high-performance devices |
Suitable for flexible circuits | Suitable for medical industries |
Suitable for high-density and reliability |
Conclusion Eminent PCB manufacturers like PCB Trace Technologies Inc consider it their responsibility to provide top-quality products to their customers. Surface finish being a significant step during board manufacturing, the high quality of surface finish is a significant step in deciding the high quality of circuit boards. PCB manufacturers, therefore, make sure that the surface finish can meet the requirements of circuit boards and their end products.