Before finalizing a future printed circuit boards supplier, a lot of reviews and screening are necessary from the customer’s side. PCB Trace Technologies Inc recommends never rushing to choose a PCB manufacturing and assembly service without adequate screening by the customer. When screening, it is necessary to ask them key questions. This will not only let customers pick the most dependable manufacturer, but also prevent them from linking up with dubious ones.
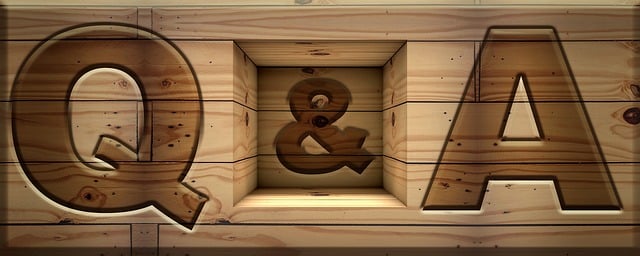
Two of the most important areas that concern customers when getting their PCBs manufactured are:
- Quality of the boards the manufacturer will deliver
- Turnaround time for the delivery
The customer must ask the manufacturer questions about their practices, processes, and certifications to make sure of getting the best quality boards after fabrication and assembly. PCB fabricators typically have a broad range of capabilities. In-depth questioning about their quality systems, processes, and compliance with international standards will reveal a wealth of information. Customers must allow their design and engineering teams adequate time to allow them to prepare key questions for the printed circuit board services. These could include:
Experience Level
Looking into the experience level of the PCB supplier. This is an important factor, since there is a greater chance that a fabricator with a vast experience has already handled the type of boards the customer requires. Inexperienced manufacturers are more likely to experiment with the requirements to gain their experience. This could not only play havoc with production timelines, but also saddle the customer with flawed PCBs. It is preferable to prioritize companies with more experience.
Questioning the manufacturer about the number of years they are in business may seem simplistic. However, it is only the beginning to opening the doors to further questions about the type of boards they have produced earlier, and whether their services match the customer’s expectations. For instance, a manufacturer may have above 20 years of experience in producing rigid boards. However, they may not be able to produce flexible boards, as they do not have that experience.
Manufacturing Facility
It is important to know if the PCB supplier has their own manufacturing facility. For instance, if they do not have their own facility, they will simply be acting as mediators, and may not be capable of providing the consistent quality of boards the customer needs. Therefore, a reliable manufacturer must not only claim to have a large manufacturing facility, but should be one who owns their manufacturing unit.
Number of Employees
Manufacturers with their own manufacturing unit must also have adequate staff to operate the facility. Appropriate staff levels allow them to sustain best practices when they handle large orders.
Another advantage with adequate number of employees is the PCB production unit can commence work on a new order without inordinate delays. For instance, if they are already running other orders, and they have maxed out their capacity, the next order must wait until they have free capacity. The increase the turnaround time may not match the customer’s production cycle.
Employee Education and Training
Even with an adequate level of staffing, there is no guarantee the output quality will be up to the customer’s requirement if the employees lack proper education and training. It is necessary the manufacturer has engineering expertise necessary for reviewing boards and making recommendations for improvement. Proper skill and training is necessary for operators to effectively handle the process machinery.
Questions about staff education and training often discloses the ability of the manufacturer to collaborate across various organizational levels, while communicating effectively.
Delivery Capabilities
It is frequently necessary for the customer to know if the manufacturer can ship to their location. Depending on the location, the fabricator may require a license to export products to other countries or to ship to a specific location, without issues. There is no point engaging in quality discussions and price negotiations if the manufacturer does not have the capability of delivering to the requisite destination.
Minimum Order Quantity
It is important to know if the PCB production unit has a minimum order requirement, and a maximum order limit. The minimum order requirement is significant if the customer is a small organization, or they are looking for a short run of a specific product. Information about the maximum order limit is necessary in case the plan is to scale up the PCB requirements in the future.
Establishing these factors in the beginning is necessary, as PCB requirements are ongoing for a company, and the customer is looking for a dependable manufacturer to meet not only the current requirements, but also their future requirements.
Cancellation Policy
It is necessary for the customer to know the cancellation policy of the PCB supplier, if they should cancel the order. The customer must make sure to have full information on the order cancellation policy before placing the order. This helps to avoid running into unpleasant surprises in case of order cancellation.
Manufacturing Philosophy
Some printed circuit board fabrication units place higher priority on delivering products quickly at low costs. Others value effectiveness and factor stakeholder requirements in their decisions. The difference between being efficient and effective lies in the way manufacturers involve in process control.
Process Control
The customer must know whether the manufacturer will align their processes to meet the requirements of the board’s shape, layout, materials, and components. This is important as the decision will also impact the sub-processes involved in the manufacturing stages.
The manufacturer’s processes must ultimately lead to matching the customer’s design specifications with the necessary precision and accuracy. They must take time to know whether the manufacturer has the ability to create accurate images, has the equipment to maintain a precise alignment of layers in multilayer boards. Whether they can accurately etch each layer, drill vias and mounting holes with precision, and provide the board with the necessary surface finish.
Technology
The customer may need to take decisions about electronic components, thereby impacting PCB assembly stages. For instance, they may have to choose between using through-hole components and surface mount components for their board. The manufacturer must have appropriate equipment to handle the technology. For surface mount components, the manufacturer must have the proper pick-and-place equipment and reflow soldering machines. For handling through-hole components, they should have auto-insertion equipment and wave soldering machines.
If the boards are for medical and aerospace applications, the customer must find out if the manufacturer has specific board cleaning technology.
Proper process control and technology application allows the manufacturer to maintain the necessary turnaround time for delivery, while ensuring a satisfactory product quality.
Inspection and Testing
To maintain a proper process control, the manufacturer must also have adequate inspection and testing procedures in place. This is necessary for error-detection and to take remedial measures on process parameters from start of manufacturing to the finish.
It is important to know what inspection methods the manufacturing process uses and where. Essential stages of inspection must involve stencil and solder paste deposition, component mounting, and soldering. This may involve manual inspection and automated optical inspection. Soldering BGA may require X-ray inspection. The customer must make sure inspection processes have the capability to detect wrong polarity, missing components, wrong components, solder shorts, insufficient solder, and or excessive solder.
It is necessary to find out about the capability of the manufacturer to conduct first article inspection. This involves destructive testing of the first few completed electronic circuit boards to ensure they are made of the specified materials and technology.
Certifications and Compliance with International Standards
Electronic circuit board manufacturers typically exhibit information about their certificates, thereby demonstrating their commitment to quality and compliance with international standards.
The customer must find out if the manufacturer complies with the ISO 9001 quality management standard. This is an international standard, and certification to this standard shows the manufacturer can meet or exceed the customer’s needs through a company-wide quality management system.
If necessary for the boards, the customer must find out if the manufacturer’s products comply with IPC, UL, RoHS, WEEE, ISO 8402 and/or other specific international standards.
Compliance with Environmental Standards
The electronics industry places great importance to environmental sustainability. Most reputable manufacturers comply with RoHS standards, restricting the use of hazardous substances throughout the manufacturing process. The customer should ask about the ability of the manufacturer to treat waste water from the fabrication processes.
ESD Safeguards
ESD or electrostatic discharge is one of the major causes of initial failure of electronics assembly. Static electricity accumulating on operator clothing can discharge through electronic components causing latent failure that may not show up in regular testing, but cause field failures to increase.
The manufacturer must be aware of ESD and the entire manufacturing setup must have proper ESD safeguards in place, including anti-static mats and grounding arrangements. Assembly operators must wear anti-static clothes, including proper head-dress and shoes.
The customer must also find out if the manufacturer extends ESD safeguards to their warehouse or storage facility. Storage of PCBs and components before and after assembly is an important factor affecting the quality of products.
Storage and Baking
It is essential that the manufacturer uses a climate-controlled storage facility to store bare PCBs. The customer must find out if the manufacturer uses vacuum-packed, heat-sealed, moisture-barrier bags for storing PCBs. This is significant if their boards must not develop camber and twist during storage.
Medical and aerospace products may require PCBs to be thoroughly baked before assembly. If necessary for their boards, customers should find out if the manufacturer has the necessary infrastructure and machinery for baking boards.
Conclusion
With so many circuit board fabrication units to select from, it may be overwhelming for customers to pick the right one. PCB Trace Technologies Inc recommends that with judicious questioning, the task of separating the best from the others will become easier. Proper questioning will demonstrate firsthand how some manufacturers simply do not measure up to the others.