As PCB manufacturers, PCB Trace Technologies Inc. knows that the fabrication process covers a lot in terms of quality control and testing. We use several quality checks and process control in PCB production to ensure a design is manufactured at scale with high quality. However, much of this typically happens in the background, beyond the designer’s reckoning. While some tests, like board design and PCB functional testing, are typically the designer’s responsibility during prototyping, others take place when producing the boards at scale.
Irrespective of the level of testing and inspection necessary, process control in PCB production for the designer to determine the basic tests that the design must comply with and let the manufacturer know about them. We have listed here the essential PCB test requirements necessary for process control while producing PCBs.
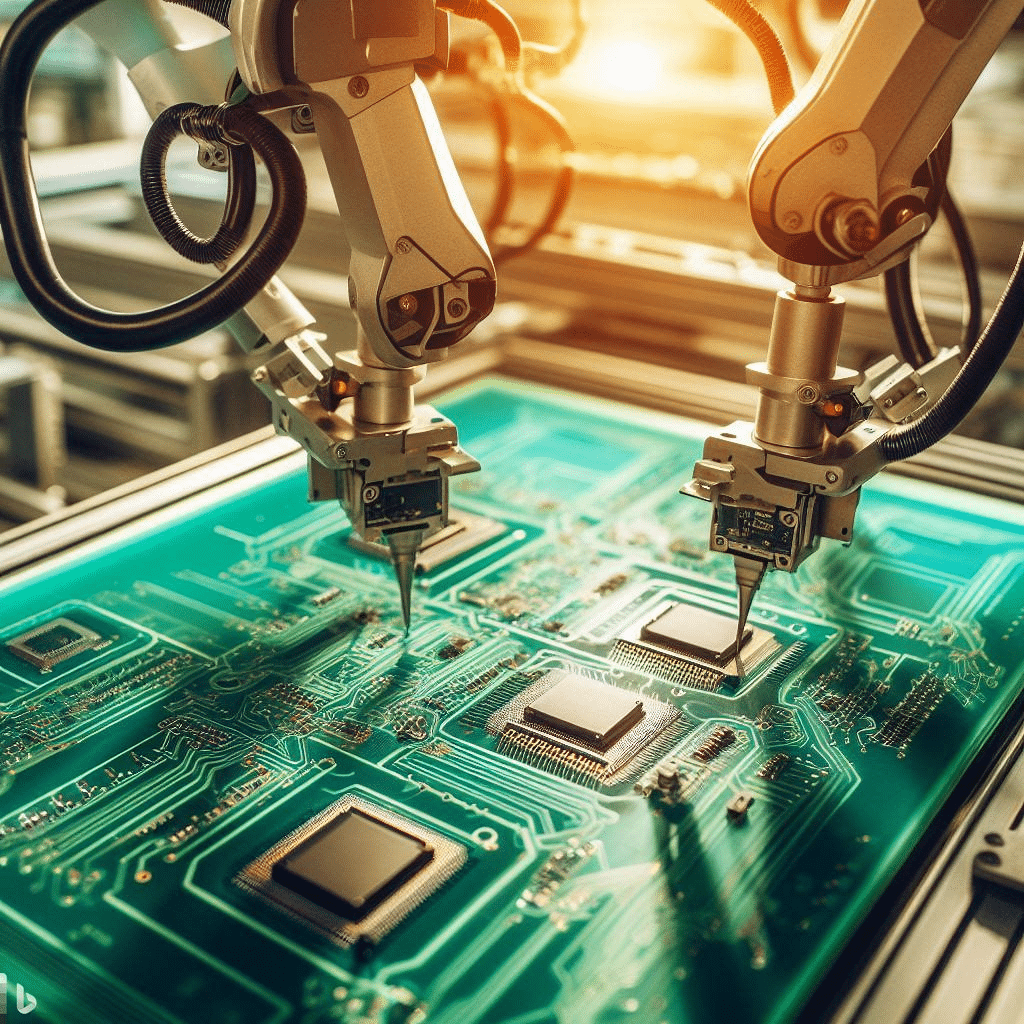
Tests during Manufacturing
Manufacturers perform numerous PCB testing procedures during the fabrication and assembly processes. While these tests help assess the quality and yield of the bare PCB, they also ensure that the design passes through the assembly without hindrance. Additionally, they also perform electrical tests during manufacturing and assembly, comparing the results with known values.
Mechanical Test and Inspection
Manufacturers perform a minimum set of mechanical tests and inspections during manufacturing to verify the process of bare board fabrication and ensure that the board assembly will be reliable.
Visual and X-Ray Inspection
While visual tests aim to identify damages like delamination and the presence of debris on the surface layers, X-rays do the same for internal layers. During assembly, an X-ray inspection is necessary for inspecting QFN or BGA packages to determine whether the connections have adequate solder and are closed. Typically, visual inspection covers the following:
- Board dimensions, thickness, surface roughness, and warpage
- Integrity and sharpness of conductive patterns, existence of debris, short circuit bridges, open circuits, burrs, and voids
- Surface quality, the existence of pits, scratches, or pin-holes on pads or traces
- Spacing between via pads and other pads and missed or inaccurately punched vias
- Via diameter compatible with design requirements
- Pad quality, including firmness, roughness, brightness, and without bulge defects
- Legend quality, firmness, clarity, cleanliness, absence of scratches, disconnection, or penetration
X-rays can have the highest defect detection rates among comparable inspection methods. The inspection method places emphasis on the long-term quality of the solder joint rather than just the connection. However, X-ray inspection can be very time-consuming and expensive. It also requires well-trained and experienced operators.
Peel Tests
This test measures the force necessary to peel apart laminations in the PCB stack-up once the fabrication is completed and it is fully cured. The test follows the standard IPC-TM-650 for copper-to-laminate peel-off and laminate-to-laminate peel-off.
PTH Inspection
The quality of the PTH or metalized vias is crucial to the proper functioning of double- and multi-layered PCBs. Quality issues related to PTH and metalized vias can create many issues, and the board may even be completely non-functional. Typical inspection of metalized vias involves checking for:
- The via wall to be smooth, complete, and free from holes or nodules
- Electrical short- and open-circuit between the pad and metalized via plating
- Resistance between via and track
- Resistance change of vias is between 5-10% after environment tests
- Quality, uniformity, and thickness of plating plane tested using metallographic analysis tests
Solder Pot and Float Tests
These tests gauge the solderability of PTH or plated through holes and whether the barrel of the PTH can withstand thermal stress during soldering without damage.
AOI or Automated Optical Inspection
This test spots assembly defects automatically. It can check for insufficient solder, open connections, cracked joints, tombstoning, keyholing, shorts, and more. The latest AOI methods use deep learning for spotting issues like cold joints.
The above tests can determine quality problems inherent in the manufacturing and assembly processes, the rework steps necessary, or whether a change in design is necessary to avoid a failed test.
AOI allows the identification of most major solder defects and is more accurate and consistent than manual visual inspection. Additionally, it is possible to add AOI to the production line directly for early detection of defects.
However, AOI, being a passive inspection method, can only detect surface defects. While it is possible to introduce database-based matching with AOI, the accuracy of the inspection depends on the quality of the database.
Electrical Tests
Manufacturers also conduct various electrical process control in PCB production to check for the presence of faults, deviations in impedance, and or the presence of conductive residues after soldering.
Continuity Test
These tests are conducted on bare boards by injecting DC currents to check for shorts between independent circuits and for continuity where necessary.
High-Potential Test
In these tests, a high potential is applied between different circuits on the bare board to verify there is adequate isolation between them. This is a recommended test for PCBs with thin dielectric layers and those that will operate at high voltages.
In-Circuit Tests
Conducted on assembled boards, these tests, besides checking for the presence of open and short circuits, also measure voltages and currents at specific test points. In special cases, a test fixture may be introduced to visualize a specific waveform. Additionally, electrical tests like power-on and power-off may be necessary to check for specific component faults.
ROSE or Resistivity of Solvent Extract Test
- ROSE or Resistivity of Solvent Extract Test
This is a continuity test to check the presence of any residue that may have been left over after the removal of the solder flux.
TDR or Time Domain Reflectometry Test
This test measures the controlled impedance in differential and single-ended traces. The test may require an attachment fixture and may be performed on a test board or a test coupon. Evaluation of signal integrity may require subsequent analysis and de-embedding.
For controlled impedance tests, the designer must rely on the manufacturer’s data and experience. If a controlled impedance requirement is a part of the manufacturing order, the manufacturer will confirm if they can achieve the impedance specifications for the material they will be using.
The above is a list of fundamental tests necessary to ensure successful fabrication assembly and to spot defects. Apart from the basic tests listed above, a PCB may be required to pass more stringent tests that stress the board to its limits.
PCB Stress Tests
After passing assembly, the board may need to be put through a battery of stress tests to ensure it will conform to its minimum reliability and performance requirements. These tests assess the long- and short-term reliability of the board against specific environmental conditions. Some tests are:
- Thermal Shock tests
- NEMA/FAA/FFPA Fire Safety tests
- Vibration tests
- HASS/HAL tests for Burn-in
- Electrical Stress tests
- Environmental Exposure tests
- UL Safety tests
- Other product or industry-specific tests
However, not all boards need to undergo these stress tests. Typically, manufacturers forego these tests for short prototype runs. Rather, they evaluate the boards against reliability standards using specific inspection procedures.
Reliability and PCB Failure Analysis
A lot goes into the reliability analysis and in understanding root causes of failure. If a board does not pass the above qualification tests, or it can be stressed to the point of failure, investigation is necessary to determine the root cause of the failure.
Manufacturers typically start with functional testing to determine the specific feature or capability of the failed PCB. This makes it possible to focus on the specific point in the design where the failure likely occurred. Apart from electrical testing on the board, manufacturers typically also use micro-sections to investigate the specific points in the design that have failed and to determine the mechanism of the failure.
If there is a failure occurring outside the anticipated operating conditions, the design can be considered a success, provided it is compliant with the reliability and design standards. However, designs are never invincible and likely to fail under extreme stress.
Typically, the goal is to determine whether the design is capable of performing reliably under reasonable expectations. Reliability standards address this specific point, and a reliable PCB is one that is compliant with these standards.
Qualification
Before subjecting your board to several reliability tests, designers must make sure they have started the design with reliability and safety standards in sight. IPC standards that focus on reliability are IPC-6011, IPC-6012D, and IPC-6013D.
The above standards offer specific dimensional guidelines and tolerances to which a board must adhere. Although they do not specify the dimensions of pads, traces, holes, or other features in the board, they offer a set of minimum criteria that the manufactured board must meet.
PCB Functional Tests
Functional testing includes a wide range of tests. These mainly focus on ensuring the desired user experience and end functions from the product that the designer intended. This is typically the responsibility of the design team, and they must establish this at the prototyping phase.
Typically performed at the last phases of production, functional testing serves as the final quality control procedure. The actual tests depend on specific test requirements and the complexity of the design. It may vary from a simple on-off power test to a comprehensive test complete with testing software and strict protocols.
Functional testing is flexible, manufacturers employ it as a substitute for more expensive test procedures. Functional testing simulates the actual operating environment and, therefore, may be more direct as compared to other testing methods.
However, with functional testing, it may be difficult to ascertain the cause of a defect. Moreover, functional testing may not isolate boards with a propensity to fail early in the lifecycle of the product.
Conclusion
At PCB Trace Technologies Inc., we understand there is no such thing as perfect quality in process control in PCB production. Quality is best ensured within an acceptable threshold rather than giving zero tolerance to every aspect.