Innovative engineering processes can succeed only with short and iterative development cycles. According to PCB Trace Technologies Inc, this results in high quality products that are cost-efficient, and capable of standing up to the tough competitive pressures. It is possible to find the optimal solution by pursuing several variants of the rapid product development.
Today, several tools are available for shortening the development process. Various computer programs are available that provide simulation of the actual activities, leading to a quick determination of the outcome of a certain combination of events. The engineer can try various combinations quickly to find the most desirable outcome.
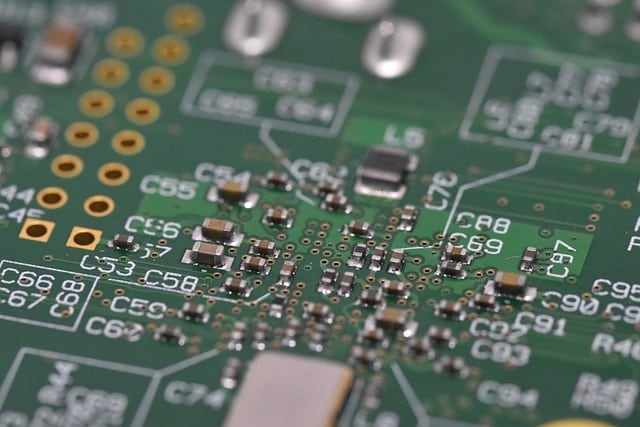
Why Rapid Product Development?
A keen international competition characterizes the market today. It involves increasingly complex products led by an extremely high innovation dynamic. In addition to the shortening of innovation cycles, the time until investments and the life cycle of products are also decreasing.
Therefore, in development, time represents the most challenging parameter. For a company to be successful, they must be fast and capable of successfully positioning new products on the market. That makes the production of prototypes very significant for a rapid product development process. For instance, depending on the quality required, it is possible to employ many generative prototyping technologies for reducing the prototyping lead times from months to a few hours.
New CAD technologies are now available for providing the possibility of checking design varieties in real-time by employing virtual reality tools. Similarly, the use of virtual prototypes, in the early phases of product development, can lead to convenient cost- and time-efficient decision-making.
What is a Prototype?
By definition, a prototype is an early model or sample of a product that can test a process or concept. The industry uses prototypes to learn if a model conforms to the design or whether its functioning responds to expectations that consumers desire. Typically, a prototype allows gathering feedback and evaluating an idea.
Prototyping Printed Circuit Boards
When designing PCBs, a designer uses software tools for rapid prototyping. Once a design team has defined the project requirements, designers engage simulation, schematic, and layout tools for developing and refining the concept into tangible processes.
Designers use simulation tools and design software to demonstrate and test various aspects of the design. Using 2-D and 3-D computer aided design tools, designers merge the mechanical and electrical aspects of the design while quickly transitioning nearer to the prototyping stage. The entire process follows a circular path where the prototype allows the designers to compare the original requirements with the outcome of the prototype, thereby providing them with a better understanding of the customers’ requirements.
Processes for Prototyping PCBs for Rapid Product Development
Rapid product development requires executing all processes first time right. This is because making mistakes leads to iterations that involve wasteful expenditure of time and resources. For this, it is important that designers follow a few good practices.
Define Project Requirements
Before the designer can start with a schematic or create a layout, they must know what the project stakeholders want. Stakeholders involve not only the customer, but also the company management, the regulatory authorities, safety and environmental statutes. For instance, a PCB design must not use hazardous material, those defined by RoHS and WEEE requirements. A PCB for a helicopter must be able to receive and transmit signals within a definitive range of frequencies that the customer specifies, but must not intrude into the frequency bands forbidden by the aviation ministry.
It is imperative to document the project requirements. The document must also include information about the environment suitable for the operation of the product. For instance, a PCB meant to control an operation in an underground mine must conform to specific tolerances to allow it to fit into pre-designed enclosures to successfully withstand vibration and moisture. Compliance to safety rules may need the designer to use special components to cater to mining applications.
Define Inter-operational Requirements
Apart from the product requirements, it is also necessary for the designer to know about the specific uses of the product, its working environment, and other issues related to inter-operational requirements. For instance, the product may need power to operate from an outside source, and it may need to integrate with other devices, operations, and systems.
For instance, a PCB for a medical equipment may have to operate in a fully closed enclosure, use a battery power source, connect to sensors to capture certain medical information. It may also have to run specific software applications, communicate with, and exchange data with other devices like Internet of Things.
The complete requirements document will then translate into a statement of work. Others in the design team may use the statement of work for establishing schedules, activities, and deliverables for the project. All this requires a collaborative understanding about the resources and effort necessary to complete the project, while providing a cost estimate for the project.
Building a Prototype for Proof-of-Concept
Designers typically use PCB design software, consisting of a broad range of tools for moving a product from the idea stage to something tangible—a prototype. They test the prototype and, if necessary, modify it, until its output fully meet the project requirements. The prototype is basically a proof-of-concept that provides evidence that the functionality and technology in the product successfully meets the project requirements.
With Design Rules and Checks, the designer establishes the parameters for the PCB. For instance, electrical rule checks ensure that the PCB has electrical functionality that functions as intended. The designer uses footprints from the component libraries that provide the best match for meeting compliance and tolerance issues. Some PCB design software packages also provide a real-time link to vendor inventories. This allows designers to pick the optimum delivery dates to match project schedules.
Matching Mechanical and Electrical Requirements
Latest PCB design software also provide 3D design tools to allow the designer to match mechanical and electrical functionality. Using these tools, the designer can ensure the PCB, along with its components, will fit within the clearance inside the enclosure. The 3D design tools also allow the designer to estimate if they require a rigid PCB, a rigid-flex board, or a totally flexible one.
Most PCB design software also support Design for Manufacturability. This speeds up the prototyping process by making the PCB easy to manufacture, with accurate design documentation. With this documentation, fabricators can process the design quickly and accurately. Such documentation typically involves Gerber files, layout diagrams, mechanical design files, and a Bill of Materials. This information is necessary to improve the collaboration between the design team and the fabricators.
Generating a Lessons Learned File
Prototypes are necessary for both design teams and stakeholders, as they provide valuable information about the product and the requirements for achieving success in the market. Before moving a prototype to the fabrication process, it may be necessary to involve steps to improve the design. At this stage of the design and prototyping stage, feedback from all stakeholders, partners, researchers, acceptance teams, and designers is very valuable.
Iterations
At this stage, it may be necessary to make the approved revisions. The design team many have to revisit the mechanical and electrical functionality of the product. Some design processes may require several iterations of feedback and testing to ensure satisfaction of all members of the team. The design team must carefully document all revisions and make the document accessible across the board.
All members of the design team benefit from a detailed and understandable design methodology. It helps to promote interaction and collaboration between the members. This collaboration also extends to researchers, user acceptance groups, and customers, while encouraging honest appraisal of the PCB design. With a good design methodology, the design team can detect errors early in the process, and make necessary modifications before finalizing the prototype.
Conclusion
While prototyping PCBs is a necessary step in the rapid product development process, PCB Trace Technologies Inc advises focusing on DFM or design for manufacturability to speed up the transition stage from prototype to product. With a smooth transition, it is possible to keep a tight control on costs, while ensuring there is clear communication between the design team, customer, and the fabricator of the PCB.