Unskilled technicians and manufacturers often encounter a common issue in printed circuit board assembly known as a cold solder. The result is a substandard product that does not perform according to expectations and definitely falls short of customer satisfaction. Being one of the most essential steps in assembling PCBs, an ineffective execution can lead not only to intermittent functioning but can also result in complete failure or even cause a fire to break out.
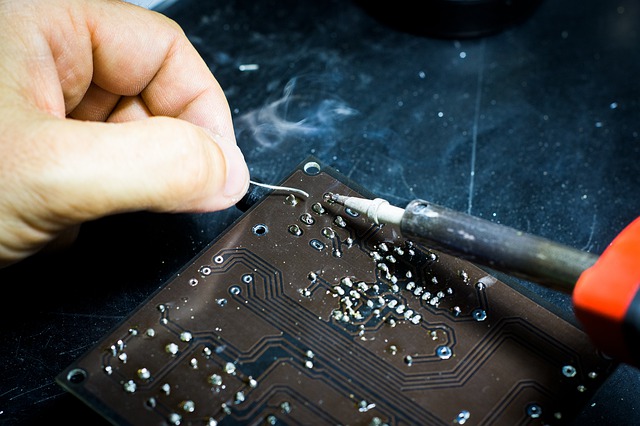
Soldering PCB Assemblies
To understand cold solder and its causes, it is necessary to know about soldering technology. Almost all electronic products contain a circuit board that holds numerous electronic components. Solder is the substance that anchors these components to the copper pads on the board. During the assembly process, solder, an alloy, melts due to the application of heat and flows between the components and their pads, effectively anchoring them to the board as it cools. Soldering may follow one of the reflow soldering, wave soldering, or manual soldering processes.
Components for Surface Mount Technology are often very small, requiring special machines for precise placement on the printed circuit board. Soldering of these components, whether reflow, wave, or manual, requires precise temperature control to obtain a clean and reliable joint, thereby allowing a proper flow of current when the board is actively functioning.
The reflow soldering process requires the deposition of solder paste between the component and the board before the oven raises the temperature. At high temperatures, the solder paste melts and flows. While cooling, the solder solidifies once again, and in the process, locks the component to the board. The reflow soldering process is primarily for soldering SMC or surface mount components onto a PCB.
The wave soldering process projects molten solder towards the component leads protruding through the copper pads on the board. The molten solder adheres to the joint. As the board moves away, the solder melts and anchors the component leads to the board. The wave soldering process is mainly for soldering THC or through-hole components.
The manual soldering process is applicable to both SMC and THCs. The instrument in use is a soldering iron with a heated tip. The operator manually places the heated tip in contact with the component and the pad to heat them up. Then they apply a solder wire to the heated joint. The heat melts the solder wire and the resulting molten solder covers the joint. On cooling, the solder solidifies, anchoring the component to the board.
What is Cold Solder?
There are two primary reasons for the occurrence of cold solder, and both are related to temperature. Cold solder can occur If the component and the pad to be soldered are not heated adequately. If the temperature is below the melting point of solder, it will not flow there will be inadequate wetting of the surfaces under soldering. The cooling solder will form lumps rather than the smooth concave surface, and the electrical conductivity of the joint may be high, or even intermittent.
Cold solder can also occur if the solder is not adequately heated. The inadequate temperature may cause the solder to soften but not flow smoothly. The cooling solder will then form lumps and the joint may not have proper electrical conductivity.
There can also be secondary reasons for cold solder formation. If the solder material is of low quality, the molten solder may be coarse, lumpy, or sloppy. This does not allow the solder to flow smoothly, and it gradually cracks while cooling, thereby reducing the electrical conductivity of the joint. The low quality of the solder may be due to sub-standard material, improperly stored solder paste, or the use of solder beyond its expiry date.
Another secondary reason for cold solder formation is the inadequate use of flux. Flux, when heated to the right temperature, causes a reduction of the oxides and oils on the solder-able surfaces, thereby making them more suitable for wetting by the molten solder. Inadequate amount of flux reduces its ability to clean the solder-able surfaces, and the molten solder is unable to wet the surfaces totally, resulting in cold solder.
For manual soldering, cold solder may be the result of an inadequately heated soldering iron, an inexperienced operator, or both. If the soldering iron is not hot enough, or the operator does not allow the tip to heat the solder-able surfaces for an adequate time, the solder wire may not melt to flow around the joint, causing a cold solder.
How to Detect and Test Cold Solder?
Primarily, a visual check is necessary. This is the simplest and the most practical process to detect a cold solder joint. As most well-formed solder joints will look even, smooth, and geometrically concave, any joint that does not comply is likely to be a cold solder joint.
For very small components, the actual solder joint may be too small to check with the naked eye. Tools like adequate lighting and a magnifying glass can be of great help here. Using a bright light and observing through a magnifying lens can reveal an uneven, lumpy, and poorly shaped joint that can be a potential cold solder joint.
For further confirmation, a resistance test is necessary. There are two ways of doing this test. The first involves measuring the resistance of the joint. Ideally, the resistance of the joint must read 0 ohms. If the multimeter shows zero or very low resistance between the component terminal and a joint adjacent to the suspected cold solder joint, then it is viable.
The other test involves setting the multimeter to continuity. If the multimeter gives a beep when connected to the component terminal and a joint adjacent to the suspected cold solder joint, then it is viable. During the above two tests, applying pressure on the suspected cold solder joint component lead may reduce or exaggerate its resistance if it is non-viable.
Repairing/Preventing a Cold Solder Joint
If there are only a few distributed occurrences of cold solder joints, using a manual soldering iron to reheat the joint will be adequate. It is necessary to use a soldering iron that has an adequately clean and heated tip. A small amount of flux may also be required to clean the surfaces of oil and oxide deposits. Finally, only an experienced operator must undertake the work.
If there are too many locations of cold solder joints on the printed board assembly, a thorough investigation of the solder quality should be in order. A check should also be made on the amount of flux applied to the board as it is going through the oven.
Lastly, it may be necessary to thoroughly review the temperature-speed profile of the board as it travels through the oven.
Conclusion
In most cases, cold solder occurs as an undesirable result of rushed and unprofessional work, typically by people trying to get the work done quickly. Cold solder issues can lead to product failure, monetary and reputational loss, and a significant erosion in customer confidence.