Across most major industries, overheating is one of the critical concerns, especially for next-generation electronics. Moore’s law states that the number of transistors on integrated chips doubles every two years. While higher transistor density does offer increased computing power, it also leads to greater thermal loads. According to PCB Trace Technologies Inc, this situation calls for a more effective thermal management.
Along with improving their performance, electronic component manufacturers also focus on device miniaturization that further complicates effective cooling. In most design cycles, handling thermal management is an afterthought, even when overheating is one of the leading causes of declining product performance. In over 55% of cases, heat is the major cause of electronic component failures. One of the methods of mitigating the devastating effects of surplus heat is by using PCB heat sinks.
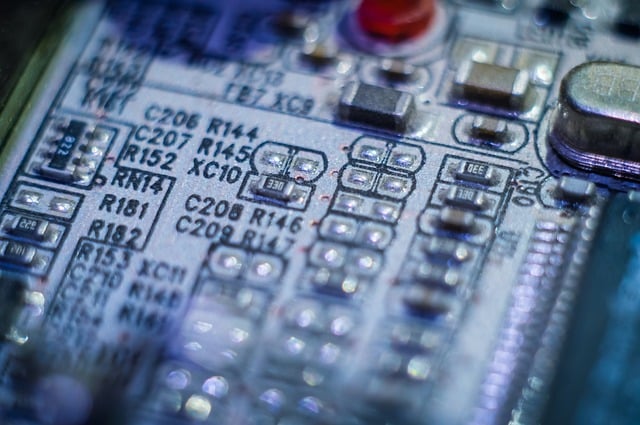
Methods of Heat Removal
According to Physics, there are three ways of removing heat:
Convection
One of the traditional ways of cooling typically consists of placing a fan next to the hot object and allowing it to blow cool air over it, thereby removing its heat. In Physics, this method of heat removal is known as convection. However, this may not be the most suitable choice in electronic devices, as many factors such as available space may restrict the deployment of a fan.
Rather than use air, convection cooling systems also use other fluids like water to improve the cooling efficiency. However, most convection cooling systems using fluids are bulky, requiring a good amount of space.
Radiation
According to Physics, all hot bodies lose heat through radiation, as they emit infrared rays or heat rays into the surroundings. This is a natural process, and requires no medium of transmission.
Conduction
The most commonly used method of heat removal in electronic systems is by conduction, using heat sinks. All materials conduct heat but at different rates. Some materials are good conductors of heat and remove heat much faster than bad conductors do. Metals are typically good conductors of heat, especially copper and aluminum, which is why most heat sinks are made of copper or aluminum.
What are Heat Sinks?
Heat sinks are passive heat-exchangers for removing heat from a hot surface via conduction and dissipating it to the surrounding atmosphere by convection. Typically, electronic systems use heat sinks made of copper or aluminum, with multiple fins to increase the available surface area for heat transfer.
Materials for Heat Sinks
Heat sinks are made from materials with high thermal conductivity like copper and aluminum. While copper has the higher thermal conductivity of the two, aluminum is preferable because of its weight and cost advantages. However, designers use the material best suited for their project, by balancing the best of both materials.
For instance, some designers use a copper baseplate to effectively conduct heat away from a hot CPU to a lightweight and cheaper aluminum heat sink. However, heat transfer between copper or aluminum heat sink to air is similar in both cases, as it involves the thermal conductivity of air. Moreover, the heat transfer advantage of copper over aluminum is not very different as expected from their thermal conductivities, which is why designers prefer aluminum as a popular material for heat sinks.
Furthermore, thermal conductivity is only one characteristic of a good heat sink. The geometry, layout, and surface area are other characteristics that squeeze out performance gains out of heat sinks. The innovation is in increasing the fin efficiency.
Fin Configuration and Efficiency
Higher the fin efficiency, better is the heat transfer via convection to the surroundings. Designers need to optimize the geometry of the fins for maximizing the air flow through the fins of the heat sink. Manufacturers use two primary fin configurations:
Pins
One of the more popular ways is to erect a forest of pins from a baseplate. This helps to maximize the surface area, and maximum performance is when the air flows along the pins axially.
Straight
Heat sinks can also have straight fins running along the entire length of the flat base to maximize the surface area. Straight fins work best when air is flowing along the length of the fins.
Heat sink manufacturers add other modifications to enhance or optimize the cooling:
Adding Fixtures
Some manufacturers use a combination of heat pipes, fans, and vapor chambers to the base heat sink to improve its efficiency.
Cross-Cut Flat Fins
Cross-cutting straight fins into multiple short sections helps to improve the transfer of heat at the surface of the fins, although it reduces the surface area of the heat sink that it exposes to the air stream. Designers use this method when the airflow is unpredictable, and they want to induce a pressure drop.
Curved Fins
By augmenting a curvature at the trailing and leading edge of a straight fin helps to provide additional movement of air molecules away from the surface of the fin. This helps in improving the air flow, and the efficiency of the heat sink.
How a Heat Sink Works?
A heat sink is basically made of a thermally conducting material, and has a large surface area. The heat sink attatches to hot components on printed circuit boards, specifically to switching devices and power transistors. The purpose of a heat sink is to absorb the heat and dissipate it.
PCB heat sinks use two principles of Physics to work—conduction and convection. Primarily it conducts heat from areas of high temperature to those at lower temperatures and lower thermal resistance. Heat sinks are made typically from aluminum or copper, both with excellent thermal conductivity and low thermal resistance. This allows heat to travel easily from a hot component to the heat sink.
The process of heat transfer is as follows:
- A PCB component generates heat when operating.
- The heat travels through the body of the component to the contact area on the heat sink.
- Lower thermal resistance allows heat to transfer from the hot component to the heat sink.
- Temperature of the hot component decreases, while the temperature of the heat sink increases.
- Heat travels through the body of the heat sink to the pins or straight fins on the heat sink.
- Presence of cold air surrounding the pins of the heat sink allows heat transfer from the pin surface to the cold air.
- Temperature of the heat sink decreases while that of the air surrounding it increases.
- Fans move the hot air from the heat sink, replacing it with cool air.
- The entire cycle repeats, stabilizing the temperatures of the component and the heat sink.
Why Use a Heat Sink?
Most modern PCB applications demand complex circuitry with high density of components. These often consume large amounts of power, and may generate more heat than the PCB can naturally dissipate, requiring the addition of a heat sink.
Some applications, like military and other mission-critical applications may add heat sinks to improve the reliability and extend the longevity of their boards. There are many advantages in using heat sinks:
Thermal Management
The heat sink primarily improves the thermal management of a PCB. Heat sinks help to solve the most critical heat dissipation problems.
Reliability
Heat sinks improve the reliability of a board through proper thermal management. By not allowing the temperatures of hot components to rise above critical levels, heat sinks help to improve the longevity of PCB boards.
Cost
Heat sinks are mostly low cost, and provide an economical solution to dissipating the excess heat in a system.
Weight
Most thermal management solutions, like fans and heat pipes, are bulky and large. In comparison, PCB heat sinks are made of copper or aluminum, and hence, lightweight, while providing excellent heat dissipating solutions.
How to Select the Right Heat Sink?
Adding a heat sink to a PCB impacts its design. If the heat sink is large, some components may have to be moved to create space for accommodating it. The height of the heat sink may require redesign of the cabinet housing the board. Here are some factors that the designer may need to consider when selecting a heat sink:
Check Thermal Requirements
The designer must know the thermal profile of the PCB component along with their optimal operating temperatures. This information is indicative of the power consumed by the component and the necessary thermal management to keep it safely in operation. The heat sink size, material, and its structure will depend on the thermal requirements.
Check Space Requirements
The design must be capable of accommodating the heat sink necessary. The designer may have to modify the material properties and dimensional features of the heat sink or the PCB design itself.
Check Heat Sink Design
After settling the requirements of the size and space for the heat sink, the designer can vary the design of the heat sink to improve its performance. For instance, the heat sink may perform better if its straight fins are placed vertically. The designer may also consider varying the number of fins and the spacing between them.
Check Mounting Technique
This is one of the most important aspects of using a heat sink, especially on a crowded PCB. As the mounting technique affects the contact area between the surface of the hot component and the surface of the heat sink, the designer must pay close attention. Any loose or uneven contact between the two surfaces will introduce air in between. Thermal conductivity of air is poorer than that of metal, and the presence of air will substantially reduce the efficiency of the heat sink.
Conclusion
After following the heat sink design basics outlined above, PCB Trace Technologies Inc recommends the designer to use PCB layout tools to place the heat sink design in 3D atop the PCB design layout. Most PCB layout tools offer verification of mechanical clearances.