The global electronic industry has been facing an acute shortage of electronic components, specifically of some categories of semiconductors and chips. This includes the intricate realm of PCB or Printed Circuit Board production. In this article, we, at PCB Trace Technologies Inc., delve into a detailed exploration of strategies for mitigating the disruptive impact of chip shortages on the PCB manufacturing process. Understanding the root causes and implementing proactive measures can help PCB manufacturers navigate through these challenges. This is important as the crisis is most serious and does not seem to have ended even as we approach the second quarter of 2024.
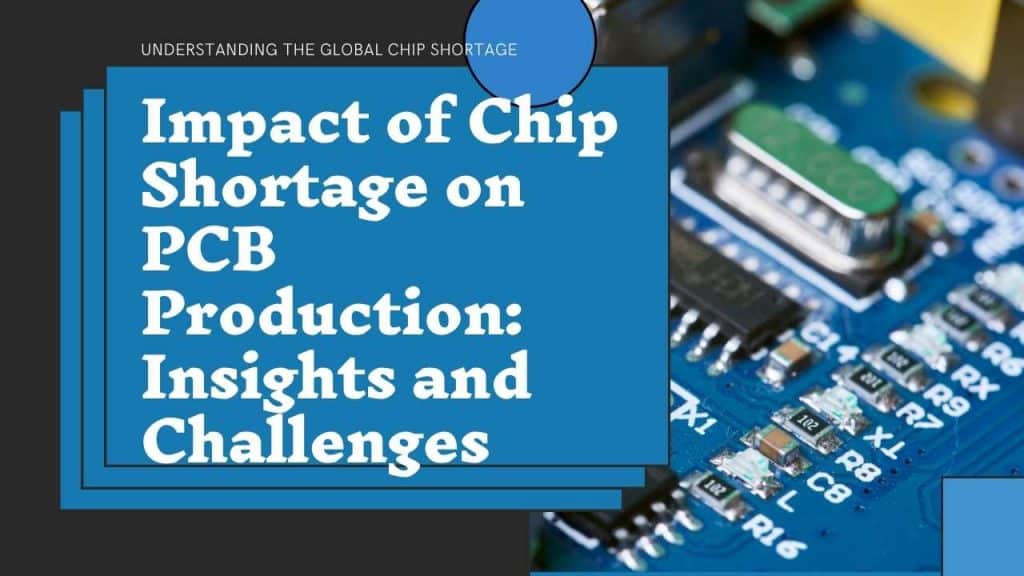
What is the Global Chip Shortage?
The global chip shortage is essentially an imbalance between demand and supply. This is especially so for components like FPGAs, CPU, and MCUs, with high integration density. The cause is primarily the growth of some sectors like 5G, IoT or the Internet of Things, and automotive sectors for the design and production of electric vehicles.
The phenomenon of chip shortage is the result of a complex interplay of factors that range from surging demand for electronic devices to disruptions in the semiconductor supply chain. Of special importance are contributors like complications in the automotive sector, heightened consumer electronics consumption, and logistical challenges that the recent pandemic has created.
How Does it Affect PCB Production?
The impact of the global shortage of electronic components has been felt across many sectors of electronic manufacturing, and this includes PCBs. For instance, engineers need to review their design process for an electronic circuit. They need to take into account from the beginning that it may be difficult to find some components, and that some components may have very long supply times.
What Caused the Component Shortage?
The global chip shortage started in 2020, triggered by the COVID-19 pandemic. Many wafer and semiconductor production lines were forced to close or temporarily suspend their production for precautionary purposes. This resulted in a drastic fall in demand for raw materials like copper, necessary for manufacturing electronic components and PCBs.
Once the electronic sector recovered from the initial shock of the pandemic, it underwent a strong recovery of the classic V type. This resulted in a rebound in the global demand for semiconductors. Although the demand for electronic components has risen very quickly, it has resulted in higher procurement costs and long delivery times.
The industry has shifted to smart working, which has increased the demand for new electronic devices. People need these devices in their homes for study and work. Therefore, the electronic industry has increased its production for quickly supplying devices like:
- Home security systems and home automation
- Home entertainment systems like video game consoles, televisions, etc.
- Remote communication systems and mobile phones, including teleconferencing systems and webcams.
- Educational systems, tablets, and laptops for teachers and students.
- Home office equipment including networking and computers
The first link in the supply chain, the wafer foundries, were the first to suffer the impact of the pandemic. The number of foundries in operation at the time was limited, and their concentration was especially in the Asian region. The largest silicon foundry controlling a large part of the wafer production in the world is TSMC or Taiwan Semiconductor Manufacturing Company. They were unable to meet the large number of orders received and therefore, could not guarantee short delivery times, at least for the next few months.
The supply of other materials also experienced a similar significant slowdown. These included materials necessary to make PCB substrates, such as copper sheets, FR-4, connectors, cables, and passive components. The increase in demand for copper sheets was due to an increase in the production of PCBs, and the need for higher quantities of components and batteries for electric vehicles.
There was also an increase in the demand for aluminum, required mainly for making MPCBs or metal-based printed circuit boards, leading to further worsening of supply problems.
More recently, the flare-up in the Russia-Ukraine conflict has also resulted in a significant increase in prices. This has limited the supply of raw materials necessary for the production of semiconductors.
With the gap between demand and supply increasing significantly, the delivery times for different types of semiconductors reached fifty weeks and beyond. Along with the lengthening of delivery times, the price of components also increased. Within the chain of electronic component development, the same pattern was observed starting from wafer production to all other stages.
What was the Impact of Global Chip Shortage on PCB Production?
The automotive industry was one of the sectors that the phenomenon of component shortages affected the most. This is primarily due to the huge number of electronic devices that the automotive industry now uses in electric vehicles. The introduction of various electronic systems in electric vehicles has led to a huge requirement for chips. These electronic systems are mainly for increasing vehicular safety by the introduction of ADAS systems, autonomous driving, and vehicular connectivity. The lack of chips has led manufacturers to reduce vehicle production, and in some cases, suspend production. This has naturally led to an increase in the price of new cars.
Other sectors have also been impacted by the shortage of chips. These include the IoT and mobile devices sector. The demand for chips for both these sectors has been growing steadily, mainly due to the introduction of new technologies like 5G and smart devices. The shortage of semiconductor wafers and various types of raw materials led to manufacturers prioritizing high-end electronic component production for automotive applications. The net result was penalization of the production of simpler components necessary for the IoT sector.
Mitigating Global Chip Shortage
The present shortage of chips has led to the conclusion that the current production of wafers is insufficient to meet global demand. Furthermore, the foundries are concentrated in a few geographical areas. To boost chip production, many foundries and manufacturers are investing heavily in building new factories. Apart from the Asian countries, such investments are likely to affect Europe and the United States. Most countries have realized that electronic components and materials are a strategic sector that offers substantial support to the economy. However, this cannot be fixed quickly. Most new production sites will achieve full capacity only by the end of 2023.
Apart from private companies, many governments are also venturing to solve the semiconductor shortage problem and prevent the consequences from happening again in the future. For instance, the US government has given its approval for the CHIPS ACT in 2022. They have allocated several billions of dollars for the research and production of chips and semiconductors in America. They intend to reduce the dependence of the US on global manufacturers for semiconductors, thereby easing the supply problems impacting the electronic and PCB industries.
In various parts of the world, countries are studying similar initiatives. For instance, the European Commission is investing several billions of euros in the European semiconductor industry. As Asia, more specifically Taiwan, is the largest producer of semiconductors, the European Commission wants to strengthen Europe’s presence in the market. Although this may not solve Europe’s immediate problems, it will be in a better position in the future.
In addition to these global initiatives, PCB manufacturers or electronic circuit designers can take better measures to tackle the problem of global chip shortage on PCB production. For instance, Infineon Technologies inaugurated its Villach plant in Austria in 2021. This is one of the most modern plants in the world, and it will produce wafers of 12 inches (300 mm).
What Can PCB Manufacturers Do?
Those involved with PCB manufacturing and assembly can apply the following actions, limiting the impact and consequences of semiconductor shortages on their business:
- Closely cooperate with electronic component and raw materials suppliers. This allows for staying aligned on technology roadmaps and investment plans, thereby ensuring the availability of materials when necessary.
- Diversify suppliers. When multiple reliable suppliers are available, it is possible to compensate for the temporary unavailability of one supplier with another. This also reduces the risk associated with concentrating procurements from a single supplier.
- Plan production well in advance. Forwarding orders to suppliers in time gives them the ability to manage their production with greater flexibility.
- Accumulate the most critical components. Components like Bluetooth and or WiFi transceivers, uncommon integrated circuits, components necessary for displays, and IoT devices, can be added to the inventory when they are available, making up for any future shortcomings.
- Rely on official distributors. Manufacturers or designers facing scarcity of components often use third-party suppliers, thereby increasing the risk of using unreliable or counterfeit components.
- Consider obsolescence. This must be considered from the initial stages of the project. Most semiconductor manufacturers provide advanced indications of a component destined for obsolescence. This aspect is important if the circuit has future developments. The same is true for components produced intermittently. To avoid possible shortages, the designer must foresee alternative components as a second or third choice.
- Consider drop-in alternatives. These are components that the designer can use to replace obsolete or non-available components. Essentially, the drop-in has the same pinout, power supply pin, and ground connection as the original.
- Recover critical components from evaluation or reference boards. This works well for the creation of demonstration or prototype PCBs, and must not be considered a permanent solution. The approach at best offers temporary relief from a situation where there is a temporary shortage of components, which will soon become available again.
Conclusion
The COVID-19 pandemic followed by the Russia-Ukraine conflict impacted negatively on the entire supply chain of electronic components and materials on a global scale.
Unless properly planned, the shortage of raw materials and components can significantly impact the design and assembly of printed circuit boards. With proper optimization of suppliers and preparation of component selection, it is possible to reduce the impact of unexpected needs of designs.
To address these challenges, and prevent future negative consequences, PCB Trace Technologies Inc. recommends the necessity to improve and increase the capacity to produce wafers, as these are the basic components necessary for all electronic circuits. PCB manufacturers and assemblers can then target actions for anticipating and mitigating any risks of possible shortages of semiconductors and raw materials.