Testing PCBs for reliability is an extensive procedure involving multiple tests. PCB manufacturers use reliability testing to identify design flaws, making it an essential process before they can offer their circuit boards to their customers. Here, at PCB Trace Technologies Inc., we offer an overview of reliability and testing strategies for mission-critical PCB applications, the methods we employ, and the testing standards we conform to.
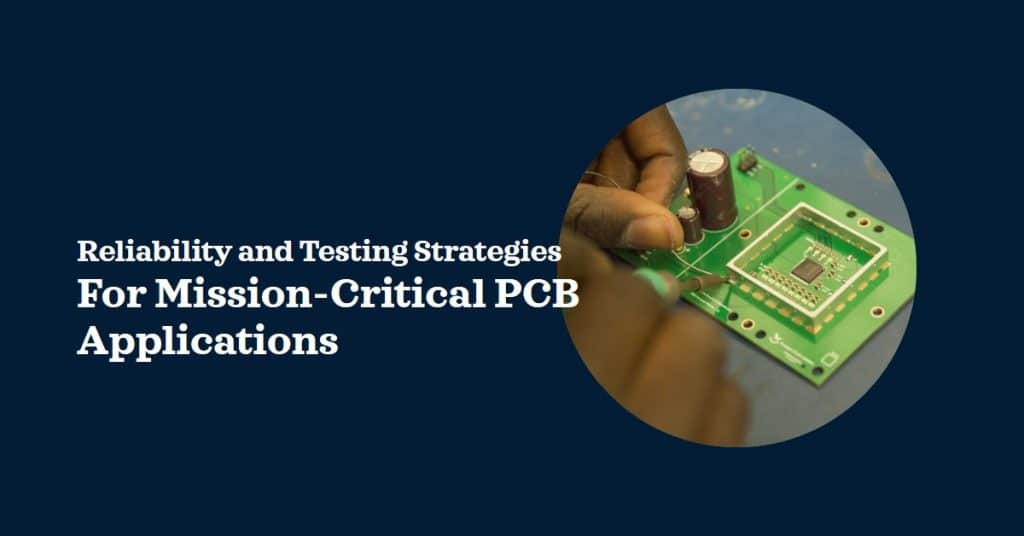
What is Reliability Testing of PCBs?
Reliability testing for a PCB is a process to identify its failure modes when it is subject to extreme conditions. That means exposing the board to various sources of stress.
By taking measurements and using the results to determine the extent and nature of damage, the tester also determines the condition levels necessary to cause harm. Sources of stress to simulate the conditions for applications include:
- Environmental conditions like dust and moisture
- Excess voltage loading
- Exposure to chemicals
- Temperature variations
- Impact and shock or vibration
Why Test a PCB for Reliability?
Testing a PCB for reliability helps to identify failure modes before large-scale production can begin. Along with the identification of failure modes, it is also necessary to know their causes, and how they happen. PCB manufacturers use the information from reliability testing to identify flawed designs, respin the flawed designs, and refine the design to prevent the occurrence of such failures in the future.
During the design process, it is almost impossible to determine the behavior of a printed circuit board in its operational environment. By testing it for reliability, the manufacturer eliminates its aging and performance problems.
Testing a PCB for reliability also indicates its nature of compliance with circuit board quality and testing standards, both regional and international. PCB manufacturers may carry out these tests on their own, or contract another company to undertake them.
Are Reliability Tests Different for Mission-Critical Applications?
In comparison to consumer electronic equipment, equipment for mission-critical PCB applications—including automotive, space, medical, and industrial—require a different approach to reliability analysis. This approach requires a better modeling of accelerated electrical aging and device degradation. It also requires studying additional phenomena that can cause shifts in device characteristics, while using realistic models to represent how the device is used.
What Reliability Tests are Applicable for Mission-Critical Applications?
1. Reducing Failure Rate Across Product Lifetime
Reducing the failure rate across the product lifetime is one of the primary challenges for mission-critical applications. Traditionally, this failure rate is known as the bathtub failure curve.
There are three regions in a bathtub curve. These are the early life, useful operating lifetime, and end-of-life regions. The curve describes the general types of failures occurring once the product reaches the consumer.
Early life failures are primarily due to defective devices that have not been identified during the test.
In the useful operating lifetime, the challenge is to ensure the device operates within its operational range necessary for reliability analysis. For instance, thermal over-stress is a specific concern.
At the end of life, failures typically occur due to device or component wear out. In this region, changes in device characteristics are primarily due to electrical stress.
Customers have a different point of view of failures as compared to that of engineers. They prefer the failure rate to be low, ideally zero, and stay zero beyond the useful operating lifetime of the product.
For instance, what is the effect if an IC in an automobile has a failure rate of 1dppm, or one defective part per million? A typical average car has about 80 ECUs or electronic control units, with each ECU containing several ICs. If the manufacturer produces several million cars, then for every million cars produced, about 1.5%, or 15,000 cars would be defective. This is certainly not acceptable.
Compared to traditional consumer application requirements, mission-critical applications place high expectations on reliability requirements over the lifetime of PCBs and other components. While typical operating lifetimes for consumer products are limited to three years at the most, mission-critical applications require at least 15 years of lifetime.
2. Overview of PCB Reliability Testing Standards
Reliability testing of PCBs broadly involves exposing the PCB assembly to extreme environmental conditions of humidity, corrosion, heat, and others. This is followed by performance tests that check whether the board has been able to withstand these conditions. When testing for reliability, there can be several sources of stress on the PCB assembly:
- Electrical loadings such as derating verification, high power, EMC, in conformation with SAE/IEC/IPC standards and UL.
- Thermal loading including climates such as thermal shock, extreme temperature, and heat flux under MIL-STD-202G and IPC-TM-650 2.6.7; thermal cycling under JEDEC JESD22-A106, IPC-9701A, and MIL-STD-883 Method 1011.
- Mechanical loading such as shock testing, vibration, and static loading under SAE/IPC/MIL-STD standards.
- Chemical loading such as chemical exposure or corrosion to match the deployment environment.
- Exposure to liquids, particles, dust, etc.
- Exposure to ionizing radiation, typically computed as TID or total ionizing doze.
- Artificial aging tests for electronic assemblies such as HATS, HASS, HALT, etc.
3. What Happens During Reliability Testing?
Assessment of PCB reliability requires conducting a set of tests focusing on each area listed above. Typically, the fabricator will perform basic fabricated board tests, which must certify the bare board to conform to requirements that the customer has specified in their fabrication notes.
4. How to Analyze PCB Failures?
Determining the limits of reliability of mission-critical PCB applications involves pinpointing failures, and determining how they arise in the device. Once a board fails, it must be investigated. Failures can arise gradually due to damage accumulated, and erratic or sudden, random or intermittent shocks. Investigation of failure modes requires the application of the above tests, involving cumulatively stressing the PCBA until failure occurs. This is followed by examining the board to identify and examine the specific failure.
Inspection Method | Failure Mode |
Optical Inspection | This method uses optical microscopes to inspect the top layers of a PCB. Optical inspection helps locate solder shorts, opens, failures, presence of solid contaminants, corrosion, and damage, |
Microsection Analysis | A thin section of the boar is cut out and inspected with either a scanning electron microscope or a regular optical microscope. This method helps to inspect roughness, vias, plating migration, and laminates. |
Contamination Testing | This method investigates specific contaminants that typically accumulate on the board when assembling. Some environments may expose the board to hazardous chemicals and require quantification of the extent to which these substances can contaminate the board. |
EDX/SEM Inspection | Sometimes a deeper inspection may be required when a microsection analysis identifies some defect on the surface of the board. To determine chemical composition, EDX is helpful. To visualize the sample, SEM or Scanning Electron Microscope is helpful. |
X-Ray Inspection | This method is for examining defects that are not immediately visible either optically, or in a microsection test. Typically useful for examining in-plane failure modes and BGA failure inspection. |
Conclusion
According to PCB Trace Technologies Inc., no PCB assembly is invincible, even for mission-critical applications. Moreover, stressing any design can eventually lead to catastrophic failure. If the applied stresses are of a level unlikely to be ever encountered during normal operation within the product’s intended environment, then the design may be considered successful from the perspective of reliability. When investigating failures and testing for reliability, it is necessary to consider and address failure modes of the device that it will most likely experience during operation.