IPC-2226 standards have many standard PCB stackups under them that support HDI PCB routing. These allow routing traces for fine-pitch components like BGA. Most standard HDI PCB stackups use buried and through-hole vias that pass through all layers. They may also use blind/buried microvias along with skip-vias on their surface layers. This allows BGA breakouts to reach the inner layers of the PCB.
PCBs continue to become thinner but contain more layers. Therefore, designers and manufacturers must use newer techniques to increase the interconnect density. One of the most complex HDI stackup and routing design styles that manufacturers are increasingly using nowadays is ELIC or Every Layer Interconnect. The idea behind this routing style is rather simple: the designer extends microvias all over the PCB stackup, allowing the routing of signals on high-density interconnects between any set of layers in the PCB. Although the idea is rather innocuous, it sets up constraints on the material sets and the manufacturing process when building the PCB.
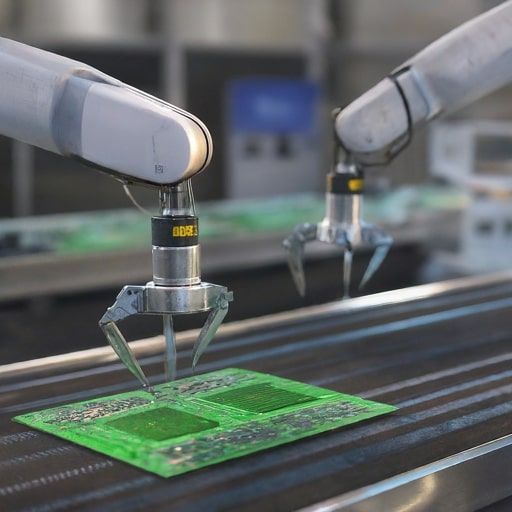
ELIC PCB Stackup
ELIC is sometimes known also as any-layer HDI, as it allows signal routing on high-density interconnects from any layer to any other layer in the stackup. These highly advanced HDI PCBs have multiple layers with in-pad microvias, filled with copper, enabling even more complex interconnections. Using ELIC, manufacturers can make HDI boards with each layer containing its own laser-drilled, copper-filled microvias. Note that ELIC uses only stacked microvias, filled with copper, to make connections between the layers. Therefore, after stacking the layers, connections are possible between any two layers in the stackup. The flexibility offered by this technique allows designers to maximize the interconnect density on any layer.
Using stacked microvias means the designer need not use any through-hole via. As all ELIC vias are copper-filled structures, there is no need for plating them. However, IPC warns against such stacked microvias spanning the entire PCB stackup as being unreliable. That is because not all fabricators can guarantee ELIC PCBs will be free from latent defects that manifest during reflow.
ELIC PCB Manufacturing
The process of manufacturing ELIC HDI PCBs starts with an ultra-thin core. The operator laser-drills microvias on the core and fills them with copper. After filling the microvias, the operator adds the next dielectric layer in sequential lamination. They then laser-drill the necessary microvias on this layer and fill them with copper. The operator repeats this sequence until they have built up the entire stack.
The number of layers in the stack can range from two to eight, although four and six-layer boards are common. Each stack layer may be of a different material or dielectric.
After the lamination of each layer, the operator etches it to remove unwanted copper and create the necessary circuit pattern. Once the operator has created the stack, they place it in a lamination press.
The sequential copper fill helps to improve the structural integrity of the board. If the PCB has stacked microvias on a layer, the operator must use a plating interface on it. Along with a strong plating interface, the sequential copper fill helps to prevent voiding/dimpling in the interior microvias.
Designers must discuss their proposed HDI board design with suitable manufacturers and implement their DFM rules so that the board will pass acceptance and quality criteria.
DFM Rules for ELIC PCBs
Apart from the DFM rules of the manufacturer, designers must also follow a few simple rules when starting with an HDI PCB that will use ELIC. These must include:
- Select the appropriate aspect ratio for microvias. This ensures the reliability of the board.
- Specify copper-filled microvias in the internal layers. This prevents dimpling/voiding.
- Select proper layer thickness with trace width and clearance for impedance-controlled lines. This allows the execution of a suitable fanout strategy.
- Ensure a symmetric layer arrangement for the entire board.
ELIC PCB Advantages
ELIC PCBs are ideal for modern devices and machines. This is because these PCBs have few complications and many advantages, including:
Increased Routing Density
Any layer interconnection in ELIC PCBs allows greater interconnect density of up to 4 times compared to that in conventional HDI boards.
Higher Design Flexibility
As ELIC PCBs allow interconnections between non-adjacent layers, they effectively remove most routing constraints, offering designers higher design flexibility.
Complex Layouts
With unrestricted layer-to-layer routing, designers can undertake highly complex layouts using advanced components.
Miniaturization
ELIC HDI PCBs allow designers to fit more functionality within a given footprint area.
Thin Stackup and Board Flexibility
As each layer in ELIC PCBs is very thin, the finished board is also thin and highly flexible. This makes ELIC PCBs very suitable for portable devices, as they can adjust to limited spaces. Their small form factor allows increased data transfer rates, making them suitable for hi-tech devices like smartwatches.
Being small and flexible, ELIC PCBs are better than rigid boards, as the former can bend and fit into limited spaces. As their component density is high, ELIC PCBs offer higher functionality as compared to rigid boards.
Superior Heat Dissipation
Rigid multilayer printed circuit boards typically suffer from heat dissipation limitations. With ELIC PCBs, it is possible to have a higher number of layers with good heat dissipation capabilities. The lower temperature rise increases the lifespan of the board.
Better Signal Integrity
With HDI routing in each layer and connectivity possible between any layer, ELIC PCBs offer better connectivity and improved signal integrity. Designers can shield any HDI layer with ground or power layers and create copper-filled microvias and skip vias to improve the conductivity and signal integrity. ELIC PCBs feature better electrical performance with low noise, reduced crosstalk, and enhanced bandwidth.
Highly Reliable
Taking less time to fabricate, ELIC HDI PCBs are highly reliable. The presence of copper-filled microvias also increases its reliability.
Better Endurance
Using better materials, ELIC HDI PCBs are more tolerant of high-temperature operation and high humidity. They show better endurance and performance in adverse environmental conditions.
ELIC PCB Challenges
Although offering many benefits over conventional PCBs, ELIC PCBs do pose some challenges as well. These include:
Higher Cost
ELIC PCBs are associated with high costs and are more challenging to manufacture compared to traditional boards.
Manufacturing Difficulties
With each layer interconnected with tiny microvias in ELIC PCBs, laminating them requires greater precision and accuracy than fabricating conventional multilayer boards.
Special Equipment
Appropriately designing and manufacturing ELIC PCBs requires special software and tools. Thin traces, tight spacing, and tiny microvias make each board layer delicate and susceptible to damage. Operators must have suitable expertise and exercise greater care when handling and assembling ELIC PCBs.
For instance, designing ELIC PCBs requires advanced PCB CAD tools for:
- Planning multiple-layer stackups
- Assigning nets to different layers
- Analyzing high-speed signal integrity
- 3-D modeling of complex space constraints
Moreover, the increased complexity of ELIC HDI PCBs demands greater coordination between layout designers, electrical engineers, and mechanical engineers.
Special Expertise
It is possible to produce multilayer boards with up to 30 or more layers with the ELIC sequential buildup process. However, special expertise may be necessary for:
Metallization
Electroplating sputtered copper in the desired thickness on each layer.
Drilling Microvias
Each layer requires drilling microvias using special lasers.
Via Filling
Filling each via with copper electroplating is necessary until the via is flush with the layer surface.
Imaging
The operator must coat each layer with a photoresist and image it to define the required trace pattern.
Additive Technologies
This requires expertise in the method the manufacturer uses to fabricate the ELIC HDI PCB. Additive technologies may use inkjet style printing, high-speed extrusion printers, FDM, Power-Bed fusion, or SLS printing methods.
Layer Bonding
Special adhesive films are necessary to bond different layers into a complete stackup.
Critical steps in the fabrication process are the accurate and precise laser-drilling of microvias and copper-filling them.
Future of ELIC PCBs
With electronic devices continually moving towards smaller sizes, higher functionality, and higher speeds, PCBs may need to increase their interconnect densities. Accordingly, more in the electronic industry will widely adopt ELIC.
Realizing the full benefits of ELIC technology will eventually depend on progress in the following key areas:
Improved Design Tools
To take advantage of ELIC’s routing flexibility, better design tools will be necessary, providing more automation and analysis features.
Scaling Microvias
With even smaller microvias, it will be possible to improve the interconnect density with better fabrication processes.
Improved Reliability
Advancements in microvia drilling, filling, and layer bonding will be necessary to improve the reliability of ELIC HDI boards.
Lower Costs
Developing better methods for volume production will make ELIC HDI boards more affordable for commercial electronic markets.
Read More: Optimum Via Size For Your PCBs – A Detailed Guide
Conclusion
ELIC HDI boards can deliver unmatched routing flexibility and interconnect density. Allowing any-to-any layer routing using microvias and skip vias, the ELIC HDI technology can accommodate extremely complex circuit connectivity and complex component layouts. This allows designers to take up innovative electronic designs for medical products, military/aerospace, IC packaging, and high-speed digital product devices. According to PCB Trace Technologies Inc., although there is a need for specialized fabrication methods, there are ongoing improvements that will spread the adoption to meet the demands for higher miniaturization and greater functionality.