HDI or High-Density Interconnect printed circuit boards need to achieve highly dense designs without compromising the functionality of the circuit. For this, designers must use the latest design strategies and manufacturing technologies. One of the techniques they use is HDI routing, which involves using multiple routing layers, smaller vias and pads, narrower traces, and thinner substrates. This allows eminent PCB manufacturers like PCB Trace Technologies Inc. to fit a high-speed, complex circuit within a small-footprint PCB.
What is HDI Routing?
Although there are plenty of designs involving 8 to 16 or more typical multilayer PCB designs, HDI routing goes far beyond that. The concepts used in HDI routing make it an entirely new discipline.
For instance, the typical PCB design treats the physical board as a single entity, dividing it into multiple layers. HDI routing, on the other hand, requires the designer to think of multiple ultrathin layers packed together to form a single functional PCB.
The evolution of vias, especially microvias, is the key catalyst to the advancement of HDI routing. Earlier, vias were copper-plated holes spanning the entire thickness of a PCB, passing through all its layers. A conventional via, therefore, drastically reduces routing areas in layers that the signal trace is not using.
Microvias, on the other hand, are laser drilled on individual layers before the operator stacks the layers. Not only are microvias significantly smaller than conventional vias, but they also span only the requisite layer, thereby preserving routing areas in other layers.
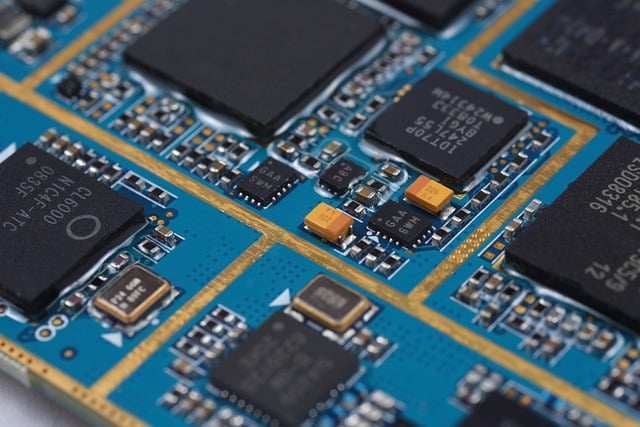
What are HDI Routing Strategies?
The use of microvias frees up routing areas in many layers, allowing PCB designers to implement complex routing. This makes it possible for them to implement strategies like any-layer HDI or every-layer interconnect. The space-saving microvias allow them to tightly populate both outer layers of a board with components, leaving the inner layers for most of the routing.
However, densely packed multiple layers with components and traces increase the risk of EMI susceptibility and emissions. Therefore, it is important to construct the PCB stackup in an HDI design appropriately. The designer must allow an adequate number of planes, both power and ground, for low-impedance return paths.
For instance, placing the inner routing layers between power and ground planes helps significantly in reducing crosstalk and cross-coupling. Designers must be careful in keeping high-speed signals, and their return paths, as short as possible. They must plan the routing carefully and use microvias strategically to limit the signal path within a small area, mainly to decrease the risk of EMI. An HDI routing strategy begins with selecting a suitable stackup.
Types of HDI PCB Stackup
Type I
This type of HDI PCB uses a single layer of HDI with laser microvias within a multilayer stackup. The rest of the layers can be of the regular type.
Although the Type I stackup does not permit buried vias, it allows blind vias and PTH or plated through-holes. Most manufacturers consider thin FR-4 dielectrics for the total number of layers, and this may contribute to deformation during temperature extremes. Moreover, for reliability, designers must aim at keeping the aspect ratio of length to hole diameter ratio to less than 10 for PTH.
Type II
This type of HDI PCB uses two layers of HDI with laser microvias within a multilayer stackup. The manufacturer places the two HDI layers one on either side of the core. The rest of the layers can be of the regular type.
Type II stackup allows using buried, blind, and micro-vias on a laminated core. It is also possible to put one or more layers of microvias on at least one of the sides. This approach is appropriate for high-density boards. It is possible to improve the effectiveness of the HDI PCB by adding more trace routing layers.
Type III
This type of HDI PCB uses four layers of HDI with laser microvias within a multilayer stackup. The manufacturer places the four HDI layers two on either side of the core. The rest of the layers can be of the regular type.
Type III has all the benefits of Type I & II and more. It is possible to use the exterior layers for power and ground terminals. The inner layers can have several microvias for improving signal routing. Stacking the vias allows even higher routing densities but increases the cost at the same time.
Designing an HDI PCB stackup is important from the manufacturing point of view. Not only must the design be practical, the manufacturer must be able to produce it effectively. The designer must design the stackup considering not only the application, but also the reliability, manufacturability, and usability of the board. That is why most HDI PCB stackup designs in the industry are of Type III.
How Microvias help HDI Routing?
HDI technology uses high-precision microvias. Manufacturers typically drill them using lasers, and the drill hole has a depth of approximately 100 µm. Because of their short barrel, microvias do not face the same challenges with different CTE values of copper and substrate as regular through-hole vias do.
Microvias do not extend throughout the thickness of a board as through-hole vias do. This provides more routing space on the other layers. Not only does this practice improve the routing density of the inner layers, but it also helps to reduce the number of signal layers necessary.
HDI PCB Routing Challenges
HDI designers often face routing challenges due to the tight spacing between traces and components. They must use proper DRC settings in their software design tools, opt for smaller packages, implement thermal management strategies, and collaborate early on with manufacturers, to navigate successfully through such challenges.
High Component Density
It can get really complex for designers when creating adequate space for routing during optimal placement of components on an HDI PCB. Dense component layouts may lead to the following potential routing challenges:
Space Constraints
As higher component and trace density are characteristic of HDI PCB, designers may face congestion and space constraints when they need to accommodate numerous components within a limited space.
Signal Integrity
Inappropriately placing components can severely impact the signal integrity of a design. For instance, placing sensitive components at the board’s edge, closer to heat-generating components, or not providing adequate clearance between components can lead to impedance mismatch, crosstalk, and or EMI susceptibility.
Thermal Management
HDI layouts are congested. Therefore, heat may be concentrated in spots, making effective thermal dissipation a concern. PCB designers must take care to place heat-generating components as far apart as possible. They must also ensure to not route critical traces like ground, data buses, and clock signals through such hotspots.
Manufacturing Complexities
Poor component placement can lead to improper routing, resulting in various manufacturing defects, such as inaccurate drill holes and misaligned layers. All this can further lead to difficulties in assembling and soldering.
Routing strategies to tackle high component density challenges must include:
- Grouping components that connect to the same signal
- Maintaining adequate spacing between components and nearby traces
- Placing specialized ICs, connectors, and high-speed components first, thereby creating shorter signal paths
- Utilizing DRC or design rule-checking tools in PCB design software
- Avoiding the use of oversized footprints
- Using more integrated components like BGAs, COBs, and SMDs
- Placing noise-sensitive components away from noise-generating components
- Employing ground planes next to sensitive signal traces
- Using round pads to route traces closer
- Placing high-current carrying components closer to the power and ground planes.
- Using separate ground planes for noisy components
- Not placing vias or components between differential pairs
Trace Impedance Mismatch
Impedance mismatch in traces causes signal integrity issues in PCBs. While this is not an issue at low to moderate frequencies, the problem exacerbates significantly with the board operating at higher frequencies. Trace impedance mismatch may be due to the following potential routing challenges:
Line Impedance
High-speed signals typically encounter line impedance mismatch when there are changes in trace widths, connectors, and vias. This can lead to signal reflections.
Crosstalk
Signal coupling in adjacent traces leads to crosstalk. The probability of crosstalk is higher in HDI boards, because of the dense routing. Crosstalk typically distorts signal, impacting overall board performance.
Skew and Timing
Uneven line impedance can be present when the signal has to travel through different layers and or unequal trace lengths, causing waveform skewing and timing misalignment. For signals carrying data, this can cause synchronization issues.
Routing strategies to tackle trace impedance mismatch must include:
- Increasing spacing between traces carrying high-speed signals
- Routing differential pairs with adequate separation
- Arranging traces prone to crosstalk at right angles to each other
- Employing TDL or twisted differential lines for differential pairs in parallel
- Surrounding sensitive traces with guard or ground traces
- Implementing length-matching techniques
- Using solid ground planes beneath and in-between layers carrying high-speed signals
- Avoiding trace routing over a void or split plane
Deficient Thermal Management
Packing components close together, as is the typical situation in HDI boards, can lead to significant heat dissipation issues. Proper heat management is necessary to prevent component degradation from overheating, leading to potent system malfunctions. Thermal management deficiencies may be due to the following potential routing challenges:
Inadequate Thermal Pathways
An HDI layout with insufficient thermal pathways can lead to the generation of localized hotspots. This, in turn, may lead to potential heat-related issues and elevated temperatures.
Thin Dielectric Material
HDI boards typically use thin dielectric material with lower thermal conductivity compared to that of thicker materials in conventional boards. Therefore, HDI materials are less effective at conducting heat away from hot components. Routing strategies must include:
Layer Stacking
High-density circuit boards typically have different layers stacked together. This includes power and ground planes, and these have a significant impact on heat conduction, distribution, and dissipation. With a proper layer arrangement, it is possible to spread the heat uniformly, thereby preventing spot heating.
Routing strategies to tackle deficient thermal management must include:
- Using thermal vias
- Using cooling fins
- Using heat sinks
- Avoiding component clustering
- Minimizing the length of high-current carrying traces
- Selecting the appropriate copper width and thickness
- Using thicker copper for ground and power planes
Read More: Why HDI PCBs Need Laser Drilling?
Conclusion
With HDI routing, it is possible to make highly complex motherboards, smartphones, graphic controllers, and other devices that are highly space-constrained. HDI routing not only allows effective use of design space, but it also helps in drastically reducing EMI issues. According to PCB Trace Technologies Inc., HDI also offers one of the greatest motivations for companies—cost reduction.