Miniaturization of the PCB or printed circuit board is among the greatest and current trends in the PCB industry. Miniaturization of electronic devices made use of special design procedures to reduce the PCB size and the footprint of electronic components that go onto it to make them denser. Over time, the development of various advanced technologies helped impact the design and processing of PCBs. According to PCB Trace Technologies Inc., demand from consumers, better and more effective production processes, and technological innovations are pushing miniaturization trends in HDI in the electronic industry. Let us consider some of these.
What is HDI PCB?
As one of the most effective technologies for PCB miniaturization, HDI or High-Density Interconnect is still an emerging technology. As suggested by the name, these special PCBs have higher component densities in comparison to traditional boards. The specialty of this technology is the designer can pack small SMC or surface mount components much closer together because the technology allows very thin traces and microvias, far smaller than those in regular boards. Not only does this help in space utilization, but it also helps minimize the board size.
Smaller and lightweight electronic products featuring higher system performance and capability expressly demand the growing technology of HDI. The compact design of the board helps in better signal integrity, with a significant reduction of signal loss and delays.
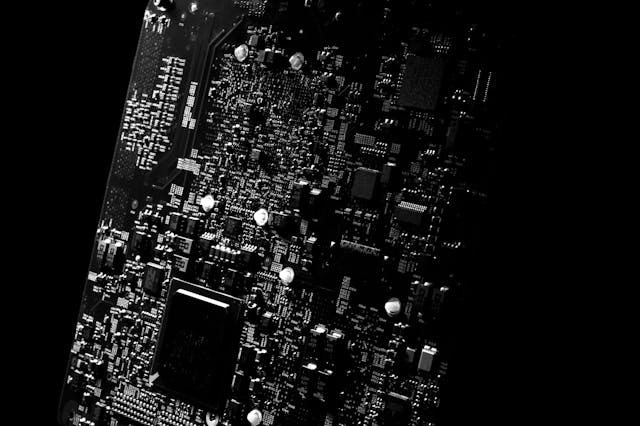
Rise of Augmented Reality
A very wide range of possibilities are now appearing in various fields due to the vast growth of AR or Augmented Reality. Various business models now apply this technology because of its main focus on real-time problems. The manufacturing industry is also slowly adopting augmented reality. AR has shown great potential in different processes in the design and manufacturing of PCBs. The PCB design industry benefits from AR with its ability to effectively design any shape. The PCB manufacturing industry benefits from AR as it helps reduce the use of materials as compared to the usual manufacturing processes. Augmented Reality also helps in another aspect of PCB design—time—providing the best possible timing in manufacturing and testing.
Internet of Things
IoT or the Internet of Things with its constituent devices interlinked with each other and the Internet, requires tiny PCBs for mounting sensors, power management, and connectivity circuitry. The major challenge with PCBs for IoT devices is they must be small, lightweight, but highly functional. Not only should the design conform to EMI rules, but it must also be robust and reliable.
One of the major requirements of the IoT industry has been low power consumption. As it is customary to station many of these tiny devices in inaccessible locations, powering them with batteries has the problem of replacement. Therefore, designers tackle this issue from two angles. They design the boards with special devices consuming very little power, and rather than power them with batteries, power them using circuits that generate power from different sources like light, radio waves, heat, etc., enabling them to be self-reliant.
The requirement of high accuracy and low power in IoT boards demands highly sophisticated design and manufacturing processes that only HDI technology can meet.
HDI PCB Design and Processing
Advanced HDI or high-density interconnect technology is driving the PCB industry with its greater wiring density per unit area, advanced MLB or multilayer boards, more layer counts, microvias, and other via technologies. The miniaturization of IC substrates like BGA and CSP is supporting this drive towards miniaturization.
Extreme miniaturization is mandatory because of increased expectations from users for higher speeds, added power, and greater functionality from miniature devices. These demands are driving PCB design and processing toward HDI, MLB, and miniature IC substrates. Not only is the above helping to produce more powerful mobile devices, but also aiding the overall proliferation of the entire electronics industry. For instance, apart from consumer electronics, miniaturization is helping the progress of AI or artificial intelligence capabilities and ADAS or advanced driver assistance systems in vehicles.
The drive towards extreme miniaturization is helping various innovative trends in PCB processing and manufacturing.
Additive HDI PCB Manufacturing
Traditionally, manufacturers have been fabricating conventional PCBs using the subtractive method. In this process, an etching process removes excess copper from copper-clad boards to achieve the final circuit pattern. This results in a substantial loss of metal.
On the other hand, additive PCB manufacturing methods add the required amount of copper to the substrate to generate the printed circuit board. It involves making a three-dimensional physical object from a digital file. By laying down progressive layers of material, a 3-D printer creates a working PCB.
Typically, the designer converts their circuit design files into CAD or computer-aided design files. The fabricator converts the CAD files into stereo lithography files that a printer can handle. There are two ways in which the fabricator uses the stereo lithography files to produce the final boards:
Ink-Jet Printing
This is basically 2-D printing, where a print head prints on an even surface using conductive ink. This method offers high resolution and consistent finish.
3-D Printing
This method depends on an extruder head to deposit conductive metal onto a substrate. The material accumulates level by level up to the desired thickness and form.
Advantages of Additive HDI PCB Manufacturing
Additive manufacturing offers several advantages over traditional methods of making PCBs.
Lead Time Reduction
Additive manufacturing methods help to cut down on the number of processes involved, thereby saving manufacturing time. For instance, manufacturing complex boards may take several days or even weeks using traditional fabrication methods. On the other hand, additive processes can effectively reduce the manufacturing time to hours.
Higher Automation
Additive methods reduce human involvement in the manufacturing process of PCBs to near zero. When fewer technicians and operators are involved, there is little room for human error requiring rework.
Enhanced Performance
With precise deposition of conductive materials, the manufacturer can ensure excellent electrical performance. The ability to minimize parasitic effects and to create smaller traces leads to improved signal integrity and overall quality and reliability.
No Minimum Quantity Required
With lower lead times, it is easier to produce a few PCBs to test a variety of design iterations. This also leads to on-demand production, where manufacturers can produce boards as needed in minimum quantities. Such flexibility not only reduces manufacturing costs, it also mitigates the risk of obsolescence. This makes additive HDI technology especially advantageous for specialized projects requiring low-volume production.
Cost and Lead Time Depend on Material Weight
Lower lead times and faster turn-around lead to cost and time becoming independent of the design complexity. This is in direct contrast to development cost and time increasing with product complexity for traditional methods.
Greater Design Freedom
Traditional manufacturing techniques often limit the designer’s freedom for precise manufacturing of their circuit designs. They may have to compromise on their vision during multilayer PCB design. On the other hand, additive manufacturing has no such limitations.
For instance, 3-D printing allows fabricating both single and multilayered boards in complex shapes and in non-planar geometries, including varied thicknesses and curves. The layer-by-layer printing process allows embedding or mounting components on non-planar substrate sides as well. Unique interconnect vias are possible, including blind, buried, micro, and in-pad types.
Sensors are an example of design freedom using 3-D printing. Designers can create customized surface topographies to place components at an angle. They can also include multiple functions in one sensor. These miniature HDI PCBs help in the improvement of the design and performance of complex projects.
As additive manufacturing works for all levels of complexity, designers can make prototypes closely resembling the finished product. That makes it easy to assess the product’s readiness for the market.
Environmentally Friendly
Additive HDI processes do not require toxic etchants and work at comparatively low temperatures of about 150 °C, thereby reducing power consumption. Moreover, additive PCB manufacturing uses materials that are up to 15 times thinner compared to conventional techniques. This not only reduces material consumption, it also means less waste generation during the production process.
Conclusion
In the context of PCB printers, additive HDI PCB especially, is transforming the manufacturing process. Engineers and innovators are now able to bring their ideas to life faster and at lower cost than ever before. With technology continuing to advance, eminent PCB manufacturers like PCB Trace Technologies Inc. predict the boundaries of innovation in the world of miniaturizing trends in HDI will continue to expand.