PCB Trace makes various types of printed circuit boards, ranging from single- to double- and multi-layered boards. With most designs of electronic equipment reducing in form, the use of smaller and finer-pitched components has increased substantially. PCB thickness is reducing, and soldering pads on PCBs are reducing in size to keep up with the smaller size of SMCs now under increasing use. This is substantially increasing the difficulty and challenge of manufacturing boards with SMCs.
With increasing use of highly complex SMD ICs like fine-pitch BGAs, it is imperative that the placement of these devices on the PCB pattern is highly accurate to facilitate proper soldering of all the pins. PCB designers typically resort to two types of pad designs to enable a proper seating of these BGA ICs on their pads. One of these is the copper defined pads design, also known as NSMD pads or Non-Solder Mask Defined pads. The other is SMD pads or Solder Mask Defined pads.
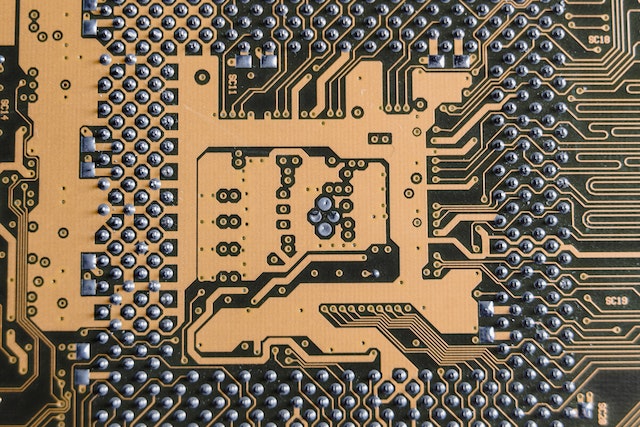
Copper Defined Pads Design
It is easy to identify a copper defined pads design, as the solder mask opening is bigger than the size of the copper pad. Such pads have their advantages and disadvantages.
Advantages Of Copper Defined Pad Design
Better Soldering Strength
Copper defined pads have the advantage of being exposed on all sides. This allows solder to adhere to the surrounding sides of the pad also in addition to the top surface, resulting in a stronger joint.
Better Pad Size Control
The PCB fabricator has a better control over the size of the soldering pad and its location. With optical exposure registering of the copper pad, this is a more accurate technology.
Higher Density
As the copper pads can be made as small as possible, it is possible to assemble ICs of higher pitch. It is possible for the designer to route multiple traces between two pads, resulting in higher component density on the board.
Disadvantages of Copper Defined Pad Design
Easier Peel Off
As the soldering adheres to the entire pad, including its sides, the pad is vulnerable to peel off due to external stress. The smaller size of the pad also contributes to lower the bonded strength of the pad to the board. For instance, there are greater chances of BGA balls cracking during impact drop tests.
PCB assemblers often use underfill glue to improve the bonding between the BGA IC and the board. However, this increases the manufacturing costs, wasting material and labor. BGA ICs with underfill are more difficult to repair.
To counter the above problems, designers use another design, the solder mask defined pad.
Solder Mask Defined Pads
The major deviation from non-solder mask defined pads is that the copper pad is larger than the solder mask. The actual soldering area is thus defined by the size of the solder mask opening, hence the name. However, these pads also have their advantages and disadvantages.
Advantages of Solder Mask Defined Pad Design
Better Pad Bonding
As the copper pads are larger, there is a stronger bonding between the pad and the board—reducing chances of peel off.
Better Performance
Because of larger pad size, failure due to impact drop reduces drastically. In fact, impact drop tests show a 53% improvement over the NSMD pad design.
Disadvantages of Solder Mask Defined Pad Design
Lower Solder Strength
With soldering restricted only to the top surface of the pad, the solder strength of the joint is lower than that for NSMD pads.
Lower Positional Accuracy
Accurate control of solder mask printing is difficult. There are greater chances of the solder mask shifting due to poor tolerance control. This can result in poor positional discrepancy between BGA balls and the pads openings on the PCB. This can also affect the actual solder pad dimension on the PCB, aggravating the accuracy problem further.
Lower Density
With larger copper pads, it is difficult to achieve higher density as in boards with NSMD pad design. Larger copper pads reduce the space between the pads, thereby reducing the routing area available.
Conclusion
Comparing the performance of SMD pad and NSMD pad designs, PCB Trace advocates the use of SMD pad design, as it helps to enhance fine-pitch BGA IC soldering, even without the underfill process.