A vast majority of PCBs or printed circuit boards that electronic equipment requires are typically made from FR4 or glass epoxy. Although many users are shifting to polyimide-based flex boards, PCB Trace Technologies Inc. finds the future of PCB design trending towards paper circuit boards. That may be because PCB substrates made of paper have better characteristics compared to those made from polyimide materials. Additionally, manufacturers have developed newer technologies that substantially increase the stability and reliability of paper circuit boards. This has resulted in designers achieving better creativity with paper circuit boards, with the result that users are increasingly viewing paper circuit boards as environmentally friendly and realistic PCB design solutions.
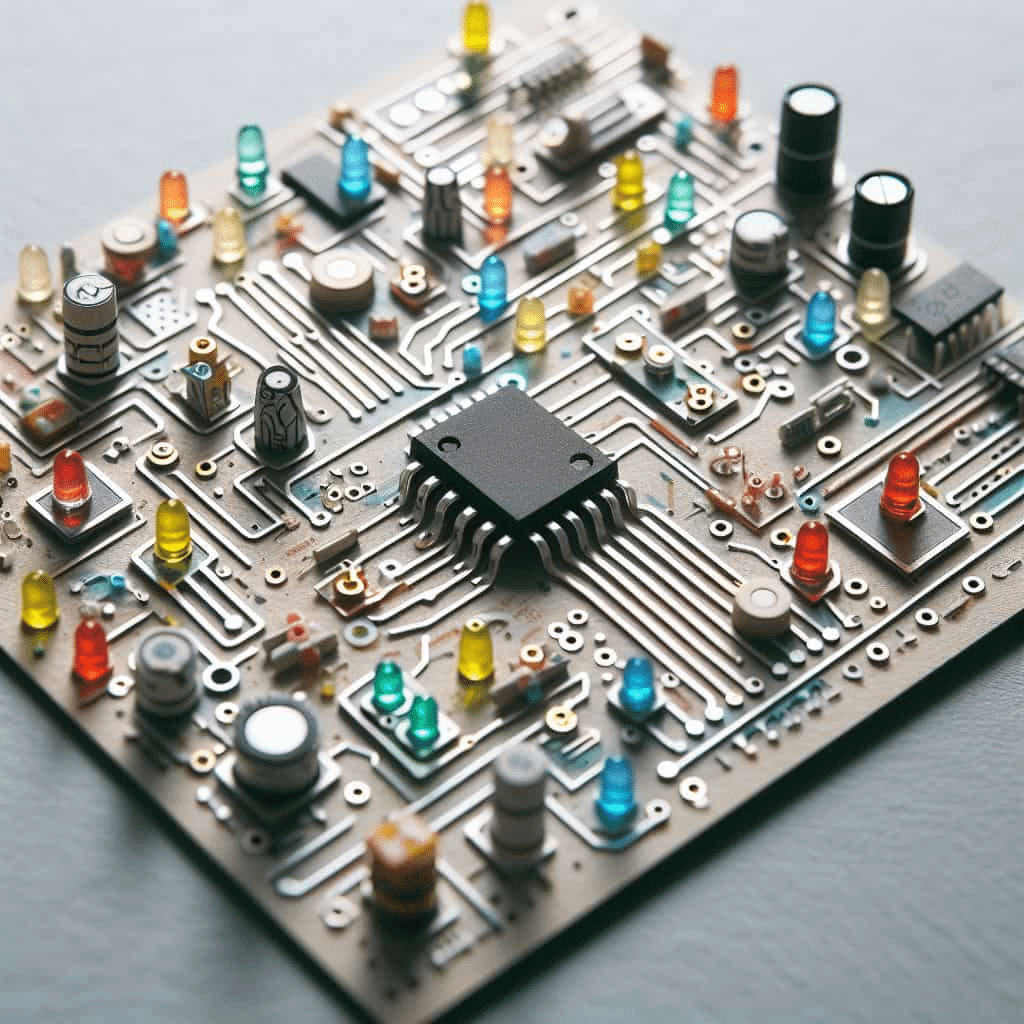
Advanced Research on Paper PCBs
Researchers have been conducting advanced research on paper PCBs for the past several years. Their efforts have culminated in the production of a transparent cellulose nano paper that can suitably function as a flexible PCB substrate. With a plasma metallization process, they were able to transform paper into solderable boards. Researchers have suitably used paper-based technologies for printing memory devices on a substrate of wrapper paper, allowing the printing of electronic components on composites made of cellulose.
Environmentally Friendly PCBs
All the above provide a glimpse of the future design of printed circuit boards for electronic equipment. Being flexible and lightweight, paper circuit boards are capable of printed intelligence. Moreover, with paper PCBs, design teams can now ensure the use of DfE or Design for Environment principles for single-use electronic equipment.
When designing single-use electronic equipment, designers must consider their effect on the environment and on human health, as specified by DfE principles. Transforming the principles from concept to reality requires a thorough assessment of the chemicals the product uses and their effect on the environment as the product reaches its end of life. Using DfE principles allows companies to follow technologies and practices that harm the environment to a minimum. According to research, manufacturing paper-based multi-layer PCBs impacts the environment substantially to a much lower degree than when manufacturing conventional PCBs. Assessing the life cycle of paper PCBs establishes the fact that their use leads to substantial improvements in the reduction or elimination of the release of toxic chemicals that increase global warming, deplete the Ozone layer, and harm life in general.
Combating e-Waste
Typically, the electronics industry has a big waste problem, often with a reference to e-waste. However, as suggested by a recent study, printed circuit boards made of paper may be a way of combating the toxic e-waste dystopia. The potential of disposable electronic products using paper, such as in paper-printed circuit boards, shows that single-use paper PCBs are the future of the electronic industry.
Rather than making PCBs from an environmentally unfriendly blend of resins, glass fibers, and metal wiring, manufacturers are making them of biodegradable paper substrates and conductive ink.
The creation process of paper PCBs is relatively simple. The steps make use of wax paper printing, infusion of metallic ink, screen printing of functional elements, laser drilling of holes and vias, and adding conductive traces. The metallic ink typically uses a mix of semiconductive and conductive formulas and is capable of forming transistors, capacitors, and resistors. All the components and printed wires on a paper PCB are equally flexible as the board itself.
Characteristics of Paper Circuit Boards
In the early days, paper PCBs had several problems. Characteristics of paper used for the boards led to conductive inks penetrating pores of the substrate, turning it into segments. Manufacturing techniques like sintering interfered with the stability of the substrate.
However, the latest research has adequately changed the characteristics of paper to make it suitable for use as a PCB substrate. Researchers changed the characteristics by applying a physical vapor deposition technique during fabrication while stacking electrically conductive structures within the paper without causing damage to the substrate.
Physical Vapor Deposition
With PVD or physical vapor deposition, researchers were able to transform material in a condensed phase to a vapor phase and subsequently into a thin film condensed phase at its atomic level. Typically, the process changes the material to vapor using a gaseous plasma or high-temperature vacuum. The PVD process then induces a pressure difference to allow the transporting of the low-pressure vapor to the substrate. Finally, the vapor condenses on the substrate to form a thin-film coating.
Researchers used the above PVD process to cover the surface of a paper substrate with a solid conductive material. They used many types of conductive materials to build up the stack for memory devices. They were able to coat the substrate with a conductive film such as aluminum oxide, yielding memory devices that exhibited excellent electrical characteristics, stability, and reproducibility.
Using paper substrates not only helps designers meet the principles of Design for Environment but also offers a substrate with a highly flexible nature that degrades minimally.
Plasma Metallization
Researchers are also using another process with promising results. This is the plasma metallization process that allows paper to function as a printed circuit board. With plasma metallization, researchers used plasma spray heads to spray powdered conductive metal at high pressure onto a base material already coated with silver paste. The hot plasma jets melt the conductive metal to enable it to combine with the silver base, forming a highly conductive substrate.
Initial experiments with plasma metallization allowed flexible printed circuits to be produced in limited quantities. Paper substrates coated with a lightweight metal cost less than substrates made of standard polyimide while exhibiting exceptional load-bearing capacity and strength. Using a flexible base material allows more creativity for designers as such researchers are showcasing the plasma metallization technique for the production of gadgets like electronic posters and postcards.
Future Applications
Researchers are continuing their work on paper PCB technology, especially on using it for large-scale production. The possibilities are endless, for instance, boards that you can easily fold, trim with scissors, or even form three-dimensional structures with military and/or medical applications.
All types of industries can benefit from these lightweight, biodegradable printed circuit boards. Manufacturers can easily make micro-sized electromechanical devices, such as ink jet-printed RFID tags, sensors printed with conductive inks, integrated printed waveguides, and other printed or embedded electronic components.
Conclusion
PCB Trace Technologies Inc. envisages that paper PCBs may not yet be suitable for computer motherboards or graphic cards. Rather, these disposable boards will be useful for wireless sensor networks and IoDT or the Internet of Disposable Things. At present, the industry is using such devices for evaluating human health, monitoring environmental conditions, tracking shipments in logistics, monitoring food and grocery systems, surveillance in the military, and in delivery systems. Moreover, as paper PCBs are susceptible to humidity, affecting their active use and shelf-life, they will need additional packaging care during shipment. While traditional electronic equipment is already susceptible to water damage, it could be disastrously messy for paper PCBs.