Solder mask or solder resist is the thin polymer coating of protective layer on a printed circuit board. It insulates the bare copper traces on the board against accidental shorts, protects against oxidation, and prevents the formation of solder bridges between closed spaced pads. Professional PCB manufacturers like PCB Trace Technologies Inc are very meticulous in solder mask fabrication, conforming to requirements of ISO 9001, UL, or RoHS standards.
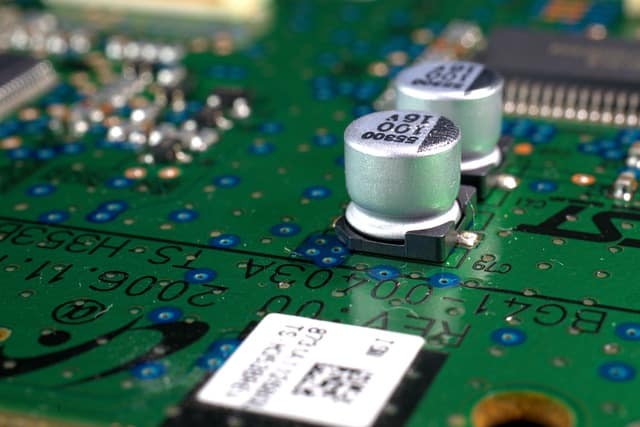
Types of PCB Solder Masks
Most solder masks consist of a polymer layer covering the metal circuits on the printed circuit board. Many types of solder mask are available, and the best choice depends on the practical application and the price. The most common choice is the use of silkscreen for printing the liquid epoxy on the board. Solder masks can be of almost any color. Three types of solder mask are common.
Liquid Epoxy Solder Mask
This is the cheapest and most common type of solder mask available. A silkscreen is necessary to print the liquid epoxy on the PCB. The silkscreen has a woven mesh for blocking the ink. The Epoxy liquid is a thermosetting polymer that hardens with thermal curing. A dye mixed with the epoxy liquid creates the required color.
Liquid Photoimageable Solder Mask
Liquid photoimageable or LPI solder mask is a more advanced type of solder mask similar to those the semiconductor manufacturers use for photoresist exposure. Operators can screen print LPI or spray it onto the PCB surface for a cheaper method of application. For more precise applications, operators use a more sophisticated method. They use a photolithographic technology for specifying the openings for pads, mounting holes, and via holes in the solder mask.
Dry Film Solder Mask
Similar to the LPI solder mask, it is necessary to expose the dry film solder mask or DFSM in a photolithography process. However, instead of a liquid application, operators must apply the dry film of the solder mask piece by piece using a vacuum substrate process. The vacuum forces the unexposed solder mask to cling to the board while removing air bubbles between the board surface and the film. After exposure, operators use a solvent to remove the unexposed areas of the solder mask, and cure the exposed film with application of heat.
Key properties of the dry film solder mask are:
- Compatible with aqueous based and no clean fluxes and solder pastes.
- Compatible with HASL, Wave soldering, roller tinning, vapor phase soldering, and reflow soldering.
- Wide processing parameters.
- Leaves a flexible scratch resistant film that improves the integrity of via hole tenting.
- Excellent capability of resolution producing straight sidewall via hole tenting.
- Has low tendency for light bleed.
- Has exceptional mechanical, physical, chemical, and electrical resistance properties due to epoxy-based chemistry.
- Suitable for use on high-density surface mount technology printed wiring board designs.
- Meets or exceeds the requirements of Bellcore, MIL P55110D, and IPC SM840C Class T&H.
Most dry film solder masks are available as high gloss, transparent, forest green films of a specified thickness, usually 75 microns (3 mils) and 100 microns (4 mils) in various widths and roll lengths. Like most dry film products, the solder mask is a photopolymer sandwiched between a polyester support sheet and a polyethylene release sheet, both of 25 microns (1 mil) thickness.
Dry Film Solder Mask General Processing Steps
Typical processing steps for applying dry film solder mask on PCBs include:
- Surface Preparation — The board surface requires thorough cleaning to guarantee no detritus is present on it.
- Hot Roll Lamination — The operator must cover both sides of the circuit board with the mask, using vacuum to remove air bubble, followed by a hot roll lamination process.
- UV Exposure — The operator places the coated board with the image film in a UV photographic developer unit. The black areas of the image film block the UV rays, while the transparent areas allow the UV rays to pass through to the coated board to develop it.
- Development — The operator rinses off the unexposed areas of the board.
- Final Cure — Application of heat for final cure.
For ensuring the optimum adhesion of the dry film solder mask, the surface of the PCB must be free of grease, oxides, dust particles, and other forms of surface contamination. The copper surface must be clean and dry, with the correct surface topography. It is recommended to clean the board surface using brush pumice, and wet brushing, followed by jet pumice application. The operator must follow this up with mains water and a DI water rinse. They must dry the boards thoroughly in a dryer machine. Applying the DFSM to an improperly dried board can result in general adhesion loss and hole tenting failure.
Selecting Dry Film Solder Mask Thickness
Dry film solder masks are available in thicknesses of 100 micron and 75 micron. The choice of the thickness to use depends on the PCB design geometry and height of the circuitry. Typically, the chosen film thickness must encapsulate all conductors on the board.
Hot Roll Lamination Conditions
Lamination of the dry film solder mask requires heat and pressure. By adjusting the pressure, it is possible to achieve a good vertical distribution of the mask, and simultaneously drive out any air trapped between tracks. Recommended temperature for hot roll is between 110 and 115 °C. The lamination process must proceed in an environment free from dust and dirt. Further processing may follow immediately after lamination. Stacking of panels after lamination must be in vertical racks and never in horizontal positions.
Exposure Conditions for Dry Film Solder Masks
Most DFSM films are negative working photopolymers that require exposure using conventional UV exposure sources of the non-collimated type. The PCBs must cool down to ambient room temperature after lamination, before the exposure can begin. Preferably, exposure of the DFSM films must take place within about 2 hours of lamination, after a hold time of about 15 to 30 minutes.
For proper polymerization of the dry film solder mask, the exposure time necessary is a function of the type and intensity of the light source the operator uses. Most films react to a spectral sensitivity ranging between 350 nm and 450 nm wavelength. To achieve acceptable exposure levels the operators must use optimum time/energy parameters.
The amount of exposure energy delivered to the film impacts its adhesion and resolution. It also affects the level of ionic contamination on the film after development and curing.
Developing the unexposed or un-polymerized dry film solder mask requires a mild alkaline solution. A thorough mains water rinsing followed by DI water rinsing is necessary after developing. Finally, a turbine dry is necessary for removing the water.
Final Cure Conditions for Dry Film Solder Masks
It is possible to obtain optimal chemical, physical, electrical, environmental, and end user assembly soldering performance properties of the dry film solder mask only after the final curing process. The final curing or cross-linking is a two-step process. It involves application of high-intensity ultraviolet light followed by a thermal curing process of approximately one hour duration at a temperature of 150 °C.
Conclusion
Eminent PCB manufacturers like PCB Trace Technologies Inc use dry film solder mask to protect the outer layers of their printed circuit boards. The high resolution of the dry film solder mask makes it highly suitable for use in high-density and fine-line circuit boards. As the solder mask is dry, it does not cause unqualified copper plating by flowing into through holes in boards. The mask also prevents formation of solder bridges during wave soldering and reflow soldering. The solder mask protects the board traces from mechanical damage and chemical corrosion.